![[반도체 공정] 식각 공정, 식각장비](https://img1.daumcdn.net/thumb/R750x0/?scode=mtistory2&fname=https%3A%2F%2Fblog.kakaocdn.net%2Fdn%2FRRmEg%2FbtsHmck1qFf%2Fxj7uvydGdT7blezf0jicaK%2Fimg.png)
안녕하세요.
식각 공정은 반도체 칩의 미세한 회로 및 패턴을 정밀하게 제작하는 데 사용됩니다. 이를 통해 반도체 칩의 기능과 성능을 향상시키고, 소자의 크기를 축소하여 더 많은 회로를 동일한 공간에 통합할 수 있습니다. 식각 공정의 정확성과 효율성은 최종 반도체 제품의 품질과 성능에 직접적으로 영향을 미치며, 현대 반도체 산업에서 핵심적인 기술로 인정받고 있습니다.
이번 시간에는 이러한 식각 공정 (Etching Process)에 대해 알아보겠습니다.
아래는 다양한 다른 반도체 공정 과정과 장비를 설명 드리고 있습니다. 참고해보세요.
0.반도체 8대 공정
https://semicircuit.tistory.com/144
1.웨이퍼 제조, 웨이퍼 제조 장비
https://semicircuit.tistory.com/17
2. 박막 공정, 박막 공정 장비
https://semicircuit.tistory.com/48
3. 패키징 공정, 패키징 장비
https://semicircuit.tistory.com/52
4. 이온 주입 공정, 이온 주입 장비
https://semicircuit.tistory.com/53
5. 플라즈마 공정, 플라즈마 장비
https://semicircuit.tistory.com/54
6. 노광 공정, 노광 장비
https://semicircuit.tistory.com/57
7. 세정 공정, 세정 장비
https://semicircuit.tistory.com/59
8. 식각 공정, 식각 장비
https://semicircuit.tistory.com/60
※1. 식각(Etching) 공정 기술
▶1. 식각 기술의 정의
: 반도체 공정에서 반도체 기판 또는 박막에 원하는 패턴을 형성하기 위해 부분적으로 또는 완전히 물질을 제거하는 공정이다. 에칭은 기판 표면에 적층된 박막 또는 마스킹 물질을 제거하여 특정 부위를 개방하고, 이를 통해 회로의 구조를 정의하거나 기판 간의 전기적 연결을 형성하는 데 사용된다.
▶2. 식각 기술의 구분
① 습식 식각 기술(Wet etching) - 등방성식각
: 적층된 물질을 액체 용액을 사용하여 부식하는 기술이다. 이 용액은 일반적으로 산성 또는 알칼리성 용액이다. 습식 식각은 화학적 에칭(chemical etching)의 일종으로 분류된다. 습식 식각 기술은 반도체 표면에 마스킹 물질을 적용한 후, 마스크를 통해 노출시킬 영역을 제외한 나머지 부분을 용액으로 제거하여 원하는 패턴을 형성한다. 이 과정은 화학 반응에 의해 진행되며, 부식 속도는 용액의 성질에 따라 결정된다. 선택비(selectivity)는 부식할 물질과 보호할 물질 사이의 선호도를 나타내는 지표이다. 선택비가 높을수록 원하는 영역만을 제거할 수 있다.
② 건식 식각 기술(Dry etching) - 이등방성식각
: 건식 식각 기술(Dry Etching)은 반도체 표면의 물질을 기체나 플라즈마를 사용하여 제거하는 기술이다. 건식 식각은 물리적 에칭(physical etching)의 한 형태로 분류된다. 건식 식각은 습식 식각에 비해 고해상도, 선택비, 깊이 제어 등 측면에서 우수한 성능을 제공한다. 또한, 건식 식각은 수직 벽면에서 발생하는 부식을 제어할 수 있어, 원하는 패턴의 형성과 정교한 회로 구조의 제조에 적합하다.
<식각 방식별 특장 비교>
* 건식 식각의 주요 파라미터
(1) 식각속도[Etch Rate: r] : 공정시간(ᐃt)을 기준으로 식각되는 박막 두께(ᐃz)의 비율로 표현된다.
(2) 이방성(Anisotropy) Aspect Ratio f : 수평성 식각 대비 수평성 식각(Horizontal etching, rh) 대비 수직성 식각(Vertical etching, rv) 비율로 표현되는 이방성 식각특성으로 f=1-(rh)/(rv)와 같이 표현된다.
(3) 선택비(Selectivity Ratio, S) 박막의 식각속도 차이를 의미하며 예를 들어 1:5(PR: SiO2)의 의미는 PR이 1만큼 식각되면 SIO2는 5가 식각된다는 것을 의미하며 소자 패턴형성에 필요한 PR 두께를 결정한다.
▶3. 건식식각(Dry etching)기술의 분류
① 물리적 건식식각(Physical Dry etching) 기술
: 물리적 건식식각은 반도체 표면을 에칭하기 위해 기체나 플라즈마를 사용한다. 이온을 가속시켜 물리적 충격으로 직접 제거하는 기술로 이온 빔 에칭 (Ion Beam Etching)과 플라즈마 에칭 (Plasma Etching)이 있다.
② 화학적 건식식각(Chemical Dry etching) 기술
: 화학적 건식식각은 반도체 표면을 화학적 반응을 통해 부식시키는 기술이다. 일반적으로 기체나 플라즈마 상태의 화학 약품을 사용하여 부식이 진행된다. 화학적 건식식각 기술에는 리액티브 이온 에칭 (Reactive Ion Etching, RIE)이 포함된다.
③ 물리화학적 식각(Physi-Chemical Dry etching) 기술
: 물리화학적 식각은 물리적인 힘과 화학적 반응을 결합한 기술로, 물리적인 조건과 화학적인 요소를 동시에 활용하여 부식을 진행한다. 이 기술은 표면 처리나 특정한 부식 패턴을 형성하는 데 사용될 수 있다. 물리화학적 식각은 다양한 방법과 환경에 따라 다양한 형태로 사용된다. 물리화학적 식각 기술은 표면 활성화, 산화, 환원 등의 화학적 반응과 동시에 기계적인 힘을 가해 부식을 진행된다. 이러한 기술은 웨이퍼 표면의 특정 영역을 처리하거나 원하는 패턴을 형성하는 데에 사용된다.
▶4. 물리화학적 식각(Physi-Chemical Dry etching) 장비
① 물리화학적 식각(Physi-Chemical Dry etching) 기술에서 반응기(Reactor)
: 식각을 위해서 식각기술 목적에 따라 ICP/TCP 플라즈마 반응기(plasma reactor), MERIE(Magnetically Enhanced RIE) 등을 사용한다.
(1) ICP/TCP 플라즈마 반응기 : ICP와 TCP 플라즈마 반응기는 고주파 전력을 사용하여 플라즈마를 생성하는 장비이다. 이러한 반응기는 RF (Radio Frequency) 전력을 사용하여 가스를 이온화하고, 플라즈마를 생성하는데에 사용된다. ICP와 TCP는 주로 균일한 플라즈마를 형성하고, 고이온 밀도를 유지하는데 특화되어 있다.
(2) MERIE 반응기 : MERIE 반응기는 이온 빔 에칭과 플라즈마 에칭을 결합한 고급 반도체 부식 장비이다. 이 반응기는 자기장을 사용하여 이온 빔을 조작하고, 플라즈마 에칭과 결합하여 에칭 공정을 제어한다. MERIE 반응기는 높은 선택적 부식, 고해상도 패턴 형성, 그리고 깊이 제어가 가능하다.
② 반도체 소자배선 박막 식각장비
: poly-crystalline Si 박막은 다결정 구조이므로 결정사이의 결합이 불완전(단결정 덩어리들의 집합)하기에 플라즈마에서 생성된 반응성 이온들이 상대적으로 낮은 이온가속도를 나타내어도 쉽게 박막들과 화학 반응을 일으킬 수 있다. 따라서 회로배선 박막 식각기술은 챔버 설계 시 높은 플라즈마 이온밀도를 구현하는 것이 빠른 식각속도를 획득할 수 있다. 대표적으로 ICP(Inductively Coupled Plasma) source를 이용한 금속막 식각장비 구성이 있다.
※2. 최신 식각(Etching)장비 개발동향
: 최신 식각장비는 다음과 같은 몇 가지 측면에서 주목할 만한 발전을 보이고 있다.
▶1. 차세대 식각장비기술(Advanced Etcher)
: 반도체생산에서 가장 요구되는 정밀한 공정 재현성을 확보하기 위해 인공지능 수준의 자동제어가 보편적으로 사용된다. 각종 진단 센서들을 챔버에 장착하고 수집된 데이터를 통해 메인제어 시스템에서 통제 관리하여 공장 시스템이 완전 무인자동화 수준으로 운영하고 있다.
▶2. 무인 자동화 감시 제어장치의 활용
: 각각의 단위공정 장비는 여러 가지 제어 알고리즘에 의해 이상 유무를 진단하고 있으며, 생산성 향상 및 미세먼지로 인한 오염방지를 위해 도입된 FOUP(Front-Opening Unified Pods)의 사용으로 FAB 내부 웨이퍼 이송에서부터 단위 공정 진행까지 완전 무인화 및 자동화가 일반화 되고 있다.
▶3. 차세대 식각 챔버 기술
: 공정가스 공급방식, RF 전원 공급장치, 웨이퍼 온도 측정, Chuck 온도 조절, Chamber wall 온도 등에서 차세대 기술을 적용하고 있다.
※3. 애싱(Ashing) 공정 기술
▶1. 애싱(Ashing) 공정의 정의
: 반도체 소자배선 형성을 위해 필요한 PR을 제거하기 위한 기술로써 탄소(Carbon)가 주요 성분인 유기화학물 및 기타 불순물을 산소 라디칼(radical)에 의한 강력한 산화 반응을 이용하여 제거하는 공정이다.
▶2. 애싱(Ashing) 공정의 분류
① 습식 애싱(Wet Ashing) 기술
: 습식 애싱은 반도체 또는 다른 물질의 표면에서 불순물을 제거하기 위해 액체 용액을 사용하는 기술이다. 일반적으로 산 또는 산화제가 포함된 용액을 사용하여 부식을 진행한다. 습식 애싱은 화학적인 반응에 의해 불순물을 용해 또는 산화시키는 방식으로 작동한다. 습식 애싱 기술은 특정한 불순물을 제거하거나 표면을 정리하는 데에 사용된다. 반도체 공정에서는 반도체 웨이퍼의 표면에 존재하는 오염물질을 제거하기 위해 주로 사용된다. 또한, 실험실에서 분석을 위해 시료의 전처리 단계에서도 습식 애싱이 사용될 수 있다.
<Ashing Sequence>
: Pre-cleaning(Main 공정 진행 전에 Wafer 표면 세정) -> Post-cleaning(Main 공정 진행 후 진행 간 발생된 Contaminati
on을 제거) -> Photo공정-> Ashing 공정(Main 공정인 Photo 공정을 거쳐 PR을 제거) -> Cleaning(Wafer에 남아있는 잔류 PR 유기물을 제거) -> Defect Cleaning(PR Strip 이후 Wafer 표면에 있는 Polymer나 Particle을 한 번 더 세정)
② 건식 애싱(Dry Ashing) 기술
: 건식 애싱은 반도체 또는 다른 물질의 표면에서 불순물을 제거하기 위해 열 또는 플라즈마를 사용하는 기술이다. 이 기술은 액체 용액 대신 열 또는 플라즈마를 이용하여 불순물을 산화시키거나 제거한다. 건식 애싱은 주로 고온 환경에서 진행되며, 열 분해 또는 산화 반응을 통해 불순물을 제거한다. 건식 애싱은 특히 유기 물질의 분해 또는 산화에 효과적이다. 반도체 제조 공정에서는 반도체 표면에 존재하는 유기 물질이나 마스킹 물질을 제거하기 위해 사용된다. 또한, 화학적으로 안정한 물질에 대한 분석을 위해 시료를 전처리하는 과정에서도 건식 애싱이 사용될 수 있다.
▶3. 건식 식각 공정 장비기술
: 플라즈마를 이용한 건식 식각장비는 식각반응이 발생하는 진공 챔버와 웨이퍼 transfer system, gas delivery system, pump system, power supply system 및 main control system과 같은 주변 장치로 구성된다.

① 전극[Electrode] : 건식 식각 공정에서 플라즈마를 생성하고 제어하기 위해 사용되는 부품이다. 전극은 주로 반도체 웨이퍼와 반응기 사이에 위치하며, RF (Radio Frequency) 전력을 인가하여 가스를 이온화시킨다. 이온화된 가스는 웨이퍼 표면에 충돌하여 식각이 진행된다.
② 웨이퍼 홀더[mechanical or electrostatic chuck] : 식각 대상 웨이퍼가 위치하는 곳으로써 식각장비에서 정밀한 온도 제어가 필요한 부품이며 웨이퍼를 안정적으로 고정하여 정확한 식각을 가능하게 한다. 웨이퍼 홀더는 웨이퍼의 크기와 형태에 맞게 설계되어야 하며, 웨이퍼의 위치를 정확하게 조절하여 식각 공정의 균일성과 반복성을 유지한다. 또한, 웨이퍼 홀더는 플라즈마 공간과 웨이퍼 사이의 간격을 제어하여 식각 조건을 조절하는 역할도 수행한다.
* 기계적 척(Mechanical Clamp Chuck) : 웨이퍼를 기계적으로 잡아준다.
* 정전기적 척(Electrostatic chuck: ESC) : 정전기를 이용해 웨이퍼를 잡아준다.
③ 가스 분산용 부품[Baffle] : 건식 식각 공정에서 사용되는 가스 유동의 방향과 분포를 제어하는 역할을 한다. Baffle은 반응기 내부에 설치되어 플라즈마 챔버의 형상과 가스 유동 경로를 조절한다. 이를 통해 플라즈마의 균일한 형성과 웨이퍼 표면에 동일한 조건의 가스 흐름을 유지할 수 있다. Baffle은 플라즈마 반응기 내의 가스 압력과 유속을 조절하여 식각 공정의 균일성과 효율성을 향상시킨다.
④ 광학윈도우[Optical Window] : 챔버 내부의 플라즈마 상태를 관찰하기 위한 투명 창으로써 석영 또는 사파이어 유리를 사용한다. 건식 식각 공정에서 사용되는 플라즈마 반응기는 고온과 화학적 환경을 가지고 있어서 광학 컴포넌트에 영향을 줄 수 있다. Optical Window는 플라즈마 반응기 내부와 외부 사이에 위치하며, 플라즈마에 노출되는 동안 광학 장치를 보호하기 위해 사용된다.
⑤ 밸브[Valve] : 상압 및 진공 상태를 분리하는 공압용 부품으로 가스의 유입 및 배출을 조절하여 원하는 식각 환경을 제공한다. 웨이퍼 수송용 개폐장치를 gate door라고도 한다.
⑥ 각종 주변 부품 : Plasma shield ring, focus ring, edge ring, pumping ring 등 존재
▶4. RF(Radio Frequency) System 구성 및 특성
: 진공 챔버에 플라즈마를 발생시키기 위한 에너지원으로 식각 장비에서는 수십 watt에서 최대 50[kW]의 에너지를 주입하며, 플라즈마 발생용으로는 13.56[MHz], 27.12[MHz], 60[MHz], 100[MHz] 등의 주파수가 사용되며, Bias 제어용으로 800[KHz], 2[MHz]가 사용된다. RF System은 RF generator, RF Matching System으로 구성된다.
① RF Generator : RF 전원을 공급하여 플라즈마 발생 또는 bias 제어용 주파수를 발진시키고 안정적인 출력을 유지시켜준다.
② RF Matching System : RF generator에서 발생시킨 에너지를 플라즈마에 공급하기 위해서 챔버와 generator 사이에서 임피던스를 맞춰주는 장치이다.
▶5. 식각장비의 주변 장치 종류 및 특성
: 식각장비는 운용을 위해 다양한 주변장치를 사용한다.
① 항온 조절기[Chiller] : 척 온도 조절을 위해 일정한 유량과 온도를 척에 냉각수를 공급하는 장치로써 척 온도를 기준으로 항온 조절기를 이용하여 실시간으로 순환 유량을 제어한다.
② 주 제어기[main controller] : 인공지능화 되어 있는 장비를 통해 운영 및 유지보수에 대한 최적화를 스스로 하고 장비와 직접 연결된 주변 장치의 통제 및 FAB 호스트와의 인터페이스 역할을 한다.
③ 웨이퍼 이송 장치[Transfer System] : 챔버 장비에서 웨이퍼 이송을 위해 사용되는 로봇 및 진공 도어를 통해 FOUP 내부 웨이퍼를 이송 진공 챔버로 이송한다.
④ 유체 공급 장치 : 식각 공정용 반응 가스를 식각장비 챔버로 공급한다.
<유체 공급 장치 구성>
(1) 유체 유량조절기(Mass Flow Controller, MFC): 각종 가스를 공압 밸브를 이용하여 통제
(2) Compressed Dry Air(CDA) 공급 장치: 각종 벨브 구동을 위해 압축 공기를 공급
(3) PCW(Pilot Cooling Water) 공급 장치: 온도 조절이 필요한 RF generator matcher 및 히터 블록의 냉각
⑤ 긴급 안전제어 장치(EMO 등) : 장비 및 사람을 보호하는 시스템으로 공정 이상발생, 정전, 쇼트, 가스 누출, 누전, 감전 및 웨이퍼 반소에러에 대하 신호를 발생한다.
▶6. 애싱 공정 장비 주요 구성 및 특성
: 애싱공정은 식각장비와는 다르게 고온 공정이므로 웨이퍼를 상온에서 조절할 수 있는 온도 제어장치가 필요하며 다양한 형태가 있다.
① Thermal Chuck Type : 전기 열선이 내장되어 애싱 공정에서 필요한 온도 영역을 균일하게 유지시켜 준다. 웨이퍼 온도 조절이 부적절하면 산화물 Sludge가 발생하여 남을 수 있어 온도조절을 중요하다.
② Lamp Heated Type : 웨이퍼 온도 조절을 램프의 빛과 열로 올리는 방식이며 자유로운 온도 조절이 가능하다. 이온 주입된 감광막 애싱 공정 기술은 이온과 감광막간 반응으로 인해 유기화합물이 형성되며 애싱 공정으로 제거해야한다.
③ 웨이퍼 냉각 스테이지 : 진공 속에서 상온으로 냉각시켜 주는 역할을 한다.
▶7. 진공 시스템
: 반도체 공정에서 플라즈마는 적절한 이온 및 순도를 유지하기 위해 진공상태 유지가 중요하며 진공 범위에 따라 다양한 종류의 진공 펌프를 사용한다.
① Mechanical Pump - 저진공 : 회전하는 부품(로터)을 통해 가스를 흡입하고 압축하여 대기압보다 낮은 압력을 유지한다. Mechanical Pump은 상대적으로 저비용이며, 일반적인 공기 펌프로서 널리 사용된다. 그러나 이러한 펌프는 고진공 환경까지는 도달하지 못하며, 한계 압력이 있다.
② Turbo Molecular Pump - 고,초고진공 : 회전하는 타입의 로터와 정적인 스테이터 블레이드로 구성되어 있다. 로터의 회전 운동은 가스 분자를 가속시켜 전진 방향으로 이동시킨다. 이로써 가스 압력을 점진적으로 감소시켜 고, 초고진공 환경을 형성한다. Turbo Molecular Pump은 매우 높은 진공 압력을 달성할 수 있으며, 반도체 제조 및 과학 연구 분야에서 널리 사용된다. 그러나 비교적 높은 비용과 민감한 구조로 인해 관리와 유지보수가 필요하다.
※4. 식각공정의 이슈 및 동향
▶1. 식각공정의 이슈
① 반도체 특수가스 국산화 선도
: 티이엠씨(TMC)는 반도체 특수가스 국산화 선도를 위해 노력하는 한국의 기업이다. 반도체 제조 공정에서는 다양한 특수가스가 필요한데, 이러한 특수가스 중 일부는 수입에 의존하고 있었다. 티이엠씨는 이러한 수입 의존도를 낮추고 국내 반도체 산업의 경쟁력을 강화하기 위해 국산 특수가스 생산 기술을 개발하고 보급하고자 하는 노력을 기울이고 있다. 이러한 가스는 노광, 식각, 이온주입, 증착 등 다양한 공정에서 사용되며 티이엠씨는 2015년 설립 이후 다양한 특수가스 국산화를 지속적으로 성공시키며, 2021년까지 연평균 73.8%라는 폭발적인 추세로 성장을 거듭해왔다. 그에 더해 2022년에는 신규 고객사를 확보하고, 전 세계적인 희귀가스 가격 폭등 속에서 3분기 기준 2,340억 원의 매출을 기록했다.
② 영우 TEL CTO "GAA 구현 차세대 식각 장비로 3나노 시장 선점"
: 도쿄일렉트론(TEL)이 게이트올어라운드(GAA) 공정, 하이 NA(High NA) 극자외선(EUV) 공정 등 차세대 3나노 반도체 장비 혁신 기술을 공개했다. 박영우 TEL코리아 최고기술책임자(CTO)는 19일 테크코리아 2022 주제 발표에서 “고선택비 식각 공정 장비를 상용화했다”며 “성능이 보다 강화된 3나노 이하 반도체 식각 장비도 개발하고 있다”고 말했다. 박 CTO는 GAA 구조에서 식각 장비 수가 증가할 것으로 전망했다. 삼성전자가 GAA 1세대(GAE)를 나노 시트 방식으로 구현하고 TSMC와 인텔이 현존 대세인 핀펫 구조 대신 GAA 독자 기술을 도입할 방침이다. TEL은 반도체 장비 제조업체로서, GAA 구현을 위한 식각 장비 개발에 주력하고 있다. GAA 구현에 필요한 고정밀 식각 공정을 제공하기 위해 기술적으로 선도적인 위치에 있는 것으로 알려져 있다. 이를 통해 TEL은 3나노 시장에서 경쟁력을 갖추고 차세대 식각 장비의 수요를 충족시키기 위해 노력하고 있다. 박영우 CTO의 언급은 TEL의 GAA 구현을 위한 식각 장비 개발에 대한 의지와 기술적 역량을 강조한 것으로 해석될 수 있다. 이러한 노력은 반도체 산업의 기술 발전과 성장에 기여할 것으로 기대된다.
③ 반도체 식각 공정용 세라믹 부품 국내 최초 개발
미국과 일본이 90%를 장악하고 있는 반도체 식각공정 장비의 부품을 우리 연구진이 국내 최초로 개발했다. 마호진 박사는 22일 "반도체 전 공정 중 식각 공정은 중국이 빠르게 추격하는 추세"라며, "이번 개발은 세계 최고 수준의 내플라즈마성 소재를 국내 기술로 개발한 대표적 사례이며, 소재 자립화를 통해 부품을 국산화하는데 도움이 될 것"이라고 말했다. 식각 공정에서는 내식성, 내구성 및 열전도성과 같은 특성을 갖춘 세라믹 부품이 필요하다. 따라서 국내 기업이 반도체 식각 공정용 세라믹 부품의 개발에 주력하고 있다면, 반도체 산업의 기술 수준 향상과 경쟁력 강화에 기여할 수 있을 것으로 기대할 수 있다.
▶2. 식각공정의 동향
① Dry 에칭의 산업 동향
: 2021년 기준 글로벌 반도체 건식 에칭 장비 시장 규모는 199억달러로 단위 공정 장비 기준 Deposition 장비(206억)와 함께 가장 큰 시장이다. 최근 6년간의 시장 성장률 기준으로는 전 장비 분야에서 가장 높은 성장률을 가진 분야이다. 반도체 공정 발전과 패턴 미세화 과정에서 식각 공정이 실질적으로 주도했음을 나타낸다.
② 기술적 에칭의 산업 개발 동향
: 물리적 식각, 화학적 식각, 물리화학적 식각 등 다양한 식각 기술을 통해 반도체 식각 공정은 지속적인 발전을 이루고 있다. 이를 위해 다음과 같은 동향이 관찰되고 있다.
(1) 고해상도 및 고정확도: 반도체 산업에서는 점점 더 작은 패턴 크기와 더 높은 정밀도가 요구된다. 따라서 고해상도 및 고정확도 식각 기술이 발전하고 있다. 고해상도 리소그래피, 레이저 식각, 전자빔 리소그래피 등의 기술이 개발되어 고밀도 반도체 장치의 제조에 적용되고 있다.
(2) 3D 구조 및 나노 패턴: 3D 실리콘 인터커넥트, 나노 패턴 제조 등과 같이 다양한 3D 구조 및 나노 패턴을 제조하기 위한 식각 기술의 연구가 진행되고 있다. 이러한 기술은 고밀도 집적회로 및 신기술 개발에 중요한 역할을 한다.
(3) 신소재 및 신기능 소자: 반도체 식각 기술은 다양한 신소재 및 신기능 소자의 제조에도 활용된다. 예를 들어, 신소재인 탄화규소(SiC) 또는 질화규소(SiN) 등의 식각 기술을 통해 고온, 고전압, 고주파 등 다양한 환경에서 작동하는 소자를 제조할 수 있다.
(4) 나노입자 및 얇은막 식각: 나노입자 식각은 나노 물질의 제조 및 응용에 중요한 역할을 한다. 반도체 산업에서는 나노입자 식각을 통해 나노소자의 제조, 광학 소자 및 센서의 제작, 에너지 저장 소자의 개발 등에 활용하고 있다. 또한, 얇은막 식각은 반도체 소자의 얇은 층을 제조하고 수정하는 기술로, 다양한 용도에 적용되고 있다.
(5) 환경 친화적인 식각 기술: 환경 보호 및 지속가능성에 대한 요구가 높아지면서, 환경 친화적인 식각 기술의 연구가 진행되고 있다. 예를 들어, 미세 입자 및 유해 물질의 배출을 줄이는 저비용, 저전력 기술의 개발이 진행되고 있다.
(6) AI 및 빅데이터 활용: 인공지능(AI) 및 빅데이터 분석 기술이 식각 공정에도 적용되고 있다. AI를 사용하여 데이터 분석 및 예측 모델을 구축하고, 빅데이터를 활용하여 공정의 최적화와 결함 예방 등에 기여하는 것이 목표이다.
(7) 플라즈마 식각 기술: 플라즈마 식각은 반도체 식각 공정에서 많이 사용되는 기술 중 하나이다. 최근에는 플라즈마 식각 기술의 발전과 함께 플라즈마 발생기술, 플라즈마 제어 기술, 식각 가스 개발 등에 대한 연구가 진행되고 있다.
(8) 새로운 재료 및 소자: 반도체 식각 기술은 다양한 재료 및 소자의 개발과 연관되어 있다. 최근에는 신소재, 유기 소자, 2D 소자 등을 포함한 다양한 소자 및 재료에 대한 식각 기술의 연구가 활발히 이루어지고 있다.
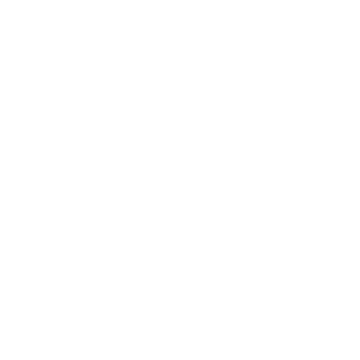
'Semiconductor > Semiconductor Fabrication' 카테고리의 다른 글
4족 원소 반도체 무엇인가? Si와 Ge의 누가 더 좋은가? (4) | 2024.10.22 |
---|---|
반도체 8대 공정: 기초부터 자세히 알아보기 (16) | 2024.10.09 |
[반도체 공정] 세정 공정, 세정 장비 (1) | 2024.05.16 |
[반도체 공정] 노광 공정, 노광 장비 (1) | 2024.05.16 |
[반도체 공정] RAM / NAND Flash / 시스템반도체 (1) | 2024.05.15 |
전자공학 블로그에 오신 것을 환영합니다! 최신 기술 동향, 회로 설계, 반도체 및 전자 부품에 대한 유용한 정보와 실습 팁을 제공합니다.