![[반도체 공정] 박막 공정, 박막 공정 장비](https://img1.daumcdn.net/thumb/R750x0/?scode=mtistory2&fname=https%3A%2F%2Fblog.kakaocdn.net%2Fdn%2Fca1guw%2FbtsHl8QrgeI%2FM2bKVnOw4A846nNdrKMkk1%2Fimg.png)
안녕하세요.
안녕하세요 이번 포스트부에서는 반도체 공정중 웨이퍼에 일정한 두께의 필름을 씌우는 과정인 박막 공정 (Thin Film Process)에 대해 알아보겠습니다.
0.반도체 8대 공정
https://semicircuit.tistory.com/144
1.웨이퍼 제조, 웨이퍼 제조 장비
https://semicircuit.tistory.com/17
2. 박막 공정, 박막 공정 장비
https://semicircuit.tistory.com/48
3. 패키징 공정, 패키징 장비
https://semicircuit.tistory.com/52
4. 이온 주입 공정, 이온 주입 장비
https://semicircuit.tistory.com/53
5. 플라즈마 공정, 플라즈마 장비
https://semicircuit.tistory.com/54
6. 노광 공정, 노광 장비
https://semicircuit.tistory.com/57
7. 세정 공정, 세정 장비
https://semicircuit.tistory.com/59
8. 식각 공정, 식각 장비
https://semicircuit.tistory.com/60
※1. 박막 기술 배경
▶1. 박막 기술 배경
: 박막공정은 기계 또는 화학적인 방법을 사용하여 일정한 두께의 박막을 원료나 부품의 표면에 코팅하는 공정을 이다. 이러한 박막은 보호, 전기적, 광학적 또는 기계적 특성을 부여하기 위해 적용된다.
박막 공정은 건식/습식, 전해/무전해, 화학/물리/용사법 등에 따라 수많은 제조 기술이 존재 한다.
▶2. 화학적기상증착(CVD: Chemical Vapor Deposition) 공정
: CVD 공정은 고체 물질을 형성하는 반응 기체를 기판 표면에 공급하고 열 또는 플라즈마 에너지를 이용하여 화학 반응을 일으켜 고체 물질 박막을 생성시킨다.
CVD 공정은 반도체 제조에서 가장 기본적인 공정 중 하나로, 증착된 박막의 두께, 합성 속도, 반응 기체의 비율 및 압력 등 다양한 조건을 조절하여 원하는 박막을 만들어낼 수 있다. 이러한 CVD 공정은 반도체 제조뿐만 아니라, 태양광 전지, 디스플레이, LED, 세라믹 등 다양한 산업에서 박막 증착에 활용되고 있다.
▶3. Sputtering 공정
: 이 공정은 고에너지 입자(ex아르곤 가스 이온)를 타깃(Target)이라 불리는 소재에 충돌시켜 원자나 분자를 제거하고, 그것들이 수집되어 다른 물체 위에 박막을 형성하도록 한다.
스퍼터링 공정에서는 고에너지 입자들이 타깃에 충돌하면 그것들은 타깃 원자나 분자를 떨어뜨리고, 이들은 진공 상태에서 물체의 다른 위치에 박막을 형성하게 된다. 이러한 박막 형성 방식은 다양한 소재에 대해서 적용 가능하며, 일반적으로는 금속, 반도체, 절연체 등의 다양한 소재를 적용할 수 있다.
▶4. ALD(Atomic Layer Deposition)
: 나노미터 규모의 박막을 생성하기 위한 공정 중 하나이다. ALD는 일종의 화학기상증착(CVD) 기술로, 분자층 복합체의 원자층 증착을 이용하여 고밀도 박막을 생성한다. ALD 공정에서는 기체 상태의 전구체가 수차례 순환되면서, 층을 쌓아나가는 방식으로 작동된다. 이 공정은 특히, 소자의 작은 크기와 높은 정밀도를 요구하는 반도체 및 나노전자소자 분야에서 매우 중요한 역할을 한다. 박막 두께 및 품질이 우수하지만 낮은 생산성을 가진다.
▶5. 박막의 목적
:박막은 절연막, 배선막, 반사막, 차폐막 등 다양한 용도로 사용된다. 절연막이나 배선막의 경우, 박막 층이 다양한 전자기기 및 반도체 장치에서 전기적인 기능을 담당한다.
배선막은 반도체 제조 공정에서 사용되는 박막의 일종으로, 반도체 칩에 필요한 배선을 만드는 역할을 한다. 반도체 칩은 아주 작은 크기를 가지고 있기 때문에, 매우 정교하게 배선이 설계되어야 한다. 소자 미세화에 따라 홀 형 컨택의 step coverage 및 종횡비(aspect ratio)가 증가하면서 점점 플러그 특성이 우수한 증착 기술, 스퍼터링, MOCVD, Metal CVD 및 ALD 기술 순서로 진화하고 있다.
절연막(insulating layer)은 반도체 소자들을 서로 분리하는 역할을 해야한다. 즉, 다양한 소자들을 구성하는데 있어 각각의 소자들이 서로 전기적으로 절연되어야 하는데, 이때 사용되는 절연층을 말한다. 간격 충진(gap fill) 성능을 향상시키기 위해 APCVD, PECVD, HDP CVD, Spin on Dielectric순으로 정밀한 층간 배선 절연막 증착기술이 적용되고 있다.
▶6. 박막(Thin Film) 공정장비
: 일반적으로 박막공정장비는 CVD, PVD, ALD, Sputtering 등의 기술을 사용한다. 이러한 박막공정장비들은 반도체 제조, 디스플레이, 태양광 산업, LED 제조, MEMS 등의 분야에서 사용된다. 박막 공정에 사용되는 모듈은 아래와 같다.
(1) 고정(Process) : 박막 공정장비의 프로세서 모듈은 공정 과정 중 박막 증착과정에서 필요한 고체 물 질을 가스나 액체 형태로 공급하고, 반응이 이루어지는 화학 반응 증착을 위해 반응 조건을 제어하는 등의 역할을 한다. 일반적으로 프로세서 모듈은 반응 증착을 위한 증착 챔버와 이를 제어하기 위한 가스 공급 시스템, 히팅 시스템, 진공 펌프 등으로 구성된다.
(2) 이송(Transfer) : 박막 공정장비의 Transfer 모듈은 박막 코팅이 완료된 웨이퍼를 이동시키는 모듈 이다. 이 모듈은 웨이퍼가 있는 캐리어를 받아서 고정하고, 원하는 위치로 이동시켜 다음 공정으로 전달한다. Transfer 모듈은 고정장치, 슬릿 밸브, 스테이지, 로봇 암 등의 부품으로 구성되어 있다.
(3) 진공(Vacuum) : 박막 공정장비의 Vacuum 모듈은 박막 증착 공정에서 필요한 진공 환경을 유지하 기 위한 모듈이다. 이 모듈은 크게 진공 챔버와 진공 펌프로 구성되어 있다.
(4 )제어(Control) : 박막 공정장비의 Control 모듈은 공정을 제어하는 중요한 역할을 수행한다. Control 모듈은 사용자가 설정한 공정 조건과 맞추어 다른 모듈들의 작동을 제어하며, 정밀한 공정 을 수행할 수 있도록 한다. SYSTEM S/W, Controller 등으로 이뤄져 있다.
▶7. 박막 공정장비 구성과 과정
(1) APCVD(Atmospheric Pressure Chemical Vapor Deposition)
: 가장 단순한 CVD 장비기술로써 대기압 기준으로 웨이퍼 표면의 열에너지와 공정 가스가 반응하여 각종 박막을 증착한다.
[구성] : 웨이퍼 반송계, 반응 가스 주입부, 반응 에너지워, 공정 챔버, 미반응 가스 배출부
<동작과정>
ㄱ. 웨이퍼 로딩: 청정한 환경에서 웨이퍼를 로딩한다.
ㄴ. 프로세스 가스 공급: 반응기 내에 가스를 유입하고, 가열로 가스를 분 해시키면서 발생하는 화학 반응에 의해 반도체 박막을 형성한다.
ㄷ. 프로세스 압력 유지: 압력을 정확하게 유지하기 위해 자동 압력제어 시스템을 사용한다.
ㄹ. 웨이퍼 반송 및 언로딩: 반응이 완료된 웨이퍼는 반송 계를 통해 다 음 공정으로 이동된다.
(2) PECVD(Plasma-Enhanced CVD)
: 플라즈마를 이용하여 반응을 촉진시키는 CVD 공정이다.
[구성] : Susceptor 장치, Shower Head 장치, Throttle Valve 장치
<동작과정>
ㄱ. 기판 적층: 기판을 적층기에 넣고, 적층 온도와 압력을 설정한다.
ㄴ. 전극 부착: 전극을 사용하여 화학 기체를 이온화시켜 플라즈마를 발생시킨다.
ㄷ. 증착: 화학 기체를 이온화된 상태로 기판 위에 분사하여 박막을 증착시킨다.
ㄹ. 후처리: 박막을 단단하게 만들기 위해 열처리나 플라즈마 후처리를 진행할 수 있다.
(3) SOG(Spin On Glass) 공정 장비
: Spin Coat 공정중 하나로 웨이퍼 표면에 스핀 코팅기를 사용하여 고분자 솔루션을 회전, 분산시키면서 코팅을 하는 과정이다.
[구성] : 스핀 코터, Silicate용액 공급장치, 희석제 공급장치 및 노즐, 고온 플레이트 장치
<동작과정>
ㄱ. Spin-On: 회전하는 플레이트에 고분자 솔루션을 떨어뜨리고, 이를 회전시키면서 고분자 솔루션이웨이퍼에 고르게 분산되도록 한다.
ㄴ. Soft Bake: Spin-On 후에는 코팅된 웨이퍼를 특정 온도에서 일정 시간 동안 굽는 공정을 진행한다. 이를 통해 솔루션 내의 남아 있는 소성 휘발성 물질을 제거하고, 고분자를 웨이퍼에 고정시킨다.
ㄷ. Cure: Soft Bake 후에는 고분자를 완전히 고정시키기 위해 고온에 서 웨이퍼를 굽는 Cure 공정을 진행한다.
ㄹ. CMP: SOG 코팅 후에는 CMP (Chemical Mechanical Planarization) 공정을 통해 불필요한 코팅 부분을 제거한다. 이를 통해 웨이퍼의 표면을 평탄하게 유지할 수 있다.
(4) 증착(Sputtering) 공정 장비
: 고에너지 입자로 원자나 이온을 고체 표면에서 제거하고 그것을 다른 고체 표면에 증착시킨다.
[구성] : 진공 펌프, 전극, RF 발생기, 가스 공급 장치, 챔버
<동작과정>
ㄱ. Deposition gas 제어: 코팅에 사용될 기체를 채워넣고, 이들의 압력과 순환량을 제어한다.
ㄴ. Target과 Substrate 배치: Target을 Chamber 내에 넣고, Substrate 를 Target 위에 위치한다.
ㄷ. 이온 충돌: Chamber 내에 흡입된 기체를 RF 전자기장이나 DC 전극 을 통해 활성화하여 플라즈마를 생성하고 플라즈마에서 생성된 이온들 은 Target을 충돌시킨다.
ㄹ. 증착: 충돌로 인해 Target의 원자나 분자들이 기체 상태로 변환되어 Substrate에 증착된다.
ㅁ. 코팅 층 성장: 증착된 원자나 분자가 서로 모이면서 Substrate 위에 코팅 층이 형성된다.
(5) MOCVD(Metal Organic CVD) 공정 장비
: 금속 박막을 적층하기 위한 공정으로, 금속 원자들이 기체 상태로 존재하며 이를 기판 위에 적층시키는 방식으로 진행된다.
[구성] : 가스 공급장치, 반응챔버, 가열 시스템, 진공시스템, 기판회전기
<동작과정>
ㄱ. 웨이퍼 로딩: 웨이퍼를 로딩한다.
ㄴ. 프로세스 가스 공급: 금속 전구체 기체를 반응실 내 에 공급한다.
ㄷ. 선량 조절: 금속 전구체 기체의 선량을 조절하여 필 요한 반응속도와 박막 특성을 얻는다.
ㄹ. 전극 반응: 금속 전구체 기체와 웨이퍼 표면의 화학 반응을 유도한다.
ㅁ. 후처리: 생성된 박막의 불순물 제거, 결합 강화 및 결함 제거 등의 후처리 단계를 거친다.
※2. ALD 공정장비
▶1. ALD 공정 장비
: ALD는 두 개 이상의 반응물을 교대로 증착시켜 나가면서 박막을 형성하는 공정이다. 반응물이 표면과 반응하여 하나의 분자층이 생성되면, 잔여 반응물과 생성된 분자층을 제거하기 위해 플라즈마 또는 고체 반응물을 이용해 정화하는 과정을 거친다.
<활용분야>
(1) 반도체 산업: 반도체 제조에서는 ALD 공정이 다이옥사이드(Dielectric)나 금속 증착 등에 사용된다.
(2) 나노전자 기술: 나노전자 기술에서는 나노 와이어 증착, 나노파티클 합성, 나노 구조 형성 등에 활용된다.
(3) 에너지 저장 기술: 배터리나 캐퍼시터 등 에너지 저장 기술에서 전극재료 증착, 전해질 코팅 등에 사용된다.
(4) 의료 분야: 의료 분야에서는 바이오 센서나 플렉서블 전자 장치 등에 적용된다.
(5) 촉매 분야: 촉매 분야에서는 촉매 증착, 촉매 코팅 등에 사용된다.
▶2. 구성
(1) Substrate Handling Module: Substrate Handling Module은 ALD 공정에서 기판을 처리하는 과정에서 사용된다. ALD 공정에서는 기판을 여러 단계에서 처리하게 되는데, 이때 Substrate Handling Module은 기판을 안전하게 이송하고, 고정하여 ALD 증착 과정에서 안정적인 기판 처리를 도와준다.
Substrate Handling Module이 포함하고 있는 다양한 구성요소 중 주요한 구성 요소로 기판을 고정하는 베드, 기판 이송을 담당하는 로봇 암, 여러 대의 기판을 동시에 처리할 수 있는 캐리어가 있다.
(2) Precursor Delivery Module: 선구자 분자를 공급하는 모듈이다. 이 모듈은 정확한 증착량을 유지하기 위해 압력 조절 및 공급 속도를 제어한다. 일반적으로, 선구자 분자는 액체 상태로 공급되며, 이를 가스 상태로 변환하는 과정이 필요하다. 이를 위해, 선구자 분자를 담은 별도의 용기가 필요하며, 이를 가열하여 증기 상태로 만든다. 그리고 이 증기는 고온, 고진공 상태에서 증착 구역으로 공급된다.
Precursor Delivery Module이 포함하고 있는 다양한 구성요소 중 주요한 구성 요소로 선구자 분자를 보관하는 용기, 선구자 분자를 가열하는 열원, 고온ᐧ고진공 상태로 선구자 분자를 증발시키는 압력 조절 장치, 다양한 선구자 분자를 사용할 수 있는 다중 채널 구조가 있다.
(3) Reaction Chamber Module: 반응이 일어나는 증착 구역이다. 여러 개의 증착 구역이 있을 수 있으며, 증착재료의 종류에 따라 다른 증착 구역을 사용할 수 있다. 반응 증착 과정에서 전자기파(Plasma)나 열과 같은 방법을 통해 반응 시간을 단축시키고, 반응을 촉진시킨다.
Reaction Chamber Module이 포함하고 있는 다양한 구성요소 중 중요한 구성 요소로 반응 증착이 이루어지는 챔버, 전자기파(Plasma) 발생 장치, 가열 장치가 있다.
(4) Vacuum System Module: 챔버 내부의 압력을 유지하는 역할을 하는 장치로 반응 챔버 내부의 공기를 제거하고 초고진공 상태를 유지시켜준다.
Vacuum System Module이 포함하고 있는 다양한 구성요소 중 중요한 구성요소로 챔버 내부의 공기를 제거하여 초고진공 상태를 유지하는 진공펌프, 챔버 내부의 압력을 측정하는 진공게이지, 챔버 내부의 압력을 제어하는 진공벨브가 있다.
(5) Heating System Module: 기판 및 증착 구역을 가열하여 증착 반응을 일으키는 모듈이다. 기판의 온도를 정밀하게 제어하는 기능을 포함된다.
Heating System Module이 포함하고 있는 다양한 구성요소 중 중요한 구성요소로 기판을 가열하는 가열체, 기판의 온도를 측정하고, 이를 제어장치에 전달하여 온도를 제어하는 온도센서(열전대), 공정에서 사용되는 기체를 기판 위에 분사하는 기체 분사기, 증착 과정에서 발생하는 열과 기체를 제거하는 배출 시스템, 온도센서에서 측정된 온도를 분석하여 가열체의 온도을 제어하는 제어장치가 있다.
(6) Plasma Treatment Module: 반도체 표면의 특정한 화학적, 물리적 특성을 변경하기 위해 플라즈마를 이용하는 모듈이다.
Plasma Treatment Module이 포함하고 있는 다양한 구성요소 중 중요한 구성요소로 플라즈마를 생성하기 위한 플라즈마 소스, 반도체 기판이 위치하고 플라즈마가 전달되어 반응이 일어나는 반응챔버, 가스를 Reaction Chamber 내부로 공급하는 가스 분사 장치, Plasma Source에 전력을 공급하는 RF 전원 공급 장치, 반응 증착 과정에서 발생하는 열과 가스를 제거하기 위한 가스 배출 시스템, 작동을 제어하는 제어장치가 있다.
▶3. 작동원리
(1) Substrate 준비: ALD 공정에서는 substrate의 표면 상태와 결합 특성이 중요하다. 일반적으로 substrate는 청정하고 부식방지 코팅을 적용하여 ALD 공정의 결과물에 영향을 미치지 않도록 한다.
(2) Substrate Cleaning: 먼저, 반도체 기판 표면을 완전히 청소한다. 이는 ALD 증착 과정에서 적층이 되는 물질과 반도체 표면 사이의 결합력을 강화하기 위함이다.
(3) Pre-processing: 기판 표면에 산화된 층을 형성하여 ALD 공정의 시작을 용이하게 한다. 이를 위해 기판을 산소, 수소 또는 산화물 가스 등에 노출한다.
(3) First Precursor Exposure: 하나의 선구체 기체(pre-cursor gas) 증착 챔버 내부로 공급하여 기판 표면에 원자층 단위로 반응 증착을 수행한다.
(3) Pre-processing: 기판 표면에 산화된 층을 형성하여 ALD 공정의 시작을 용이하게 한다. 이를 위해 기판을 산소, 수소 또는 산화물 가스 등에 노출한다.
(4) First Precursor Exposure: 하나의 선구체 기체(pre-cursor gas) 증착 챔버 내부로 공급하여 기판 표면에 원자층 단위로 반응 증착을 수행한다.
(5) Purge: 첫 번째 선구체 기체 공급 이후, 반응에 사용된 기체와 반응 생성물을 제거한다. 이 단계에서는 반응 공간에 청정 기체(대개 N2)를 공급하여 반응 생성물과 잔여 선구체를 완전히 제거한다.
(6) Second Precursor Exposure: 다음 단계에서는 두 번째 선구체 기체가 반도체 표면에 공급한다. 이 기체는 첫 번째 선구체 기체와 상호작용하여 증착 층의 두 번째 원소층을 형성 시킨다.
(7) Purge: 두 번째 선구체 기체가 반응한 후, 반응 생성물과 잔여 선구체를 완전히 제거하는 데 사용된다. 이때도 반응 공간에 청정 기체(대개 N2)를 공급한다.
(8) Cycle Repeat: 위의 과정이 한 번의 ALD 주기(Cycle)이다. 필요한 증착 층 두께가 형성될 때까지 이러한 ALD 주기를 반복한다. 층의 두께는 반응 증착과 후처리의 반복 횟수에 따라 결정된다. 일반적으로 20~100회의 반복으로 적층물이 형성된다. 이 과정에서, 선행자 및 후행자의 흐름 및 반응 시간, 반응 챔버 내부의 온도와 압력 등의 공정 변수는 정밀하게 제어되어야 한다.
(9) Post-Treatment: ALD 과정에서 증착된 박막의 물성을 개선시키기 위해 선택적으로 추가적인 처리 과정을 수행한다. Post-Treatment 과정은 다양한 방법으로 수행될 수 있지만, 일반적으로는 열처리, 플라즈마 처리, 산화 처리 등이 사용된다.
※3. 국내외 CVD/Sputter 장비회사
▶1. CVD 장비회사와 대표 장비
(1) KEIT (한국전자기술연구원)_국내
: 다양한 분야에서 연구 개발을 수행하는 국책 연구소 중 하나이다. KEIT의 CVD 기술은 다양한 소재 에 대한 광범위한 응용분야를 포함하는 다양한 기술을 제공한다.
[장비]
- K-CVD : 기계적으로 안정적인 플라즈마 공급, 고정밀한 온도 제어, 고품질 박막 형성 등의 기술을 적용한다.
- K-PVD : 반도체, 디스플레이, 태양광 산업 등 다양한 산업 분야에서 사용되는 PVD 장비이다.
- K-MOCVD : 형광체나 반도체소자 등을 제조하는 고급 반도체 산업에서 사용되는 CVD 장비이다
- K-CNT : 탄소나노튜브(CNT)를 제조하기 위한 장비이다. CNT는 고강도, 고전도성, 열전도성 등의 우수한 물성을 가지고 있어서 다양한 분야에서 응용이 가능하다.
(2) ASM International_해외
: ASM International의 CVD 기술은 핵심적으로 2D/3D NAND 플래시 메모리, DRAM, Logic/Interconnect 및 MEMS와 같은 다양한 산업 분야에서 활용된다. ASM International은 다 양한 고객의 요구에 따라 다양한 CVD 시스템을 제공한다.
[장비]
- EmerALD: 다양한 산업 분야에서 사용되는 두께가 균일하고 고도로 정교한 나노 박막 코팅을 생성할 수 있는 고급 CVD 장비이다. EmerALD는 알루미나, 이산화규소, 실리콘, 탄화규소, 질화규소 등 다양한 재료에 대해 안정 적이고 정확한 코팅이 가능하며, 웨이퍼의 직경이 200mm, 300mm 및 450mm에 대응하는 버전이 이다.
- Intrepid : 반도체, 태양 전지, LED 등에서의 박막 코팅 작업에 적합하다. Intrepid는 고온 박막 코팅을 위해 최 대 2000도의 온도에서 작동하며, 진공 환경에서 작업이 이루어진다. 이 장비는 다양한 타입의 박막 코팅을 지원하 며, 다양한 프로세스를 사용하여 여러 유형의 기능성 박막 코팅을 생성할 수 있다.
- Polygon : 다양한 응용 분야에서 고성능 및 저비용의 트랜지스터, 메모리, 통신 및 고감도 장비 등을 생산하기 위 해 사용된다. 이 장비는 특히 큰 직경의 웨이퍼를 처리할 수 있는 능력으로 알려져 있다.
▶2. Sputtering 장비회사와 대표 장비
(1) KFCT(KF Semi-Tech)_국내
: KIAT은 기존의 CVD 공정 방식과 달리 CVD 리액터 내부에서 기체 혼합이 아닌 전기방사를 이용하 여 탄화규소 박막을 형성하는 새로운 기술인 Plasma Enhanced Chemical Vapor Deposition (PECVD) 기술을 개발하였다.
[장비]
- KFCT-8000 : 대형 LCD, OLED, Solar Panel, 스마트 폰 디스플레이 패널 등의 제조에 사용된다. 이 장비는 대 형 유리 기판을 사용하여 다량의 증착을 수행하며, 증착률이 빠르고 높은 증착 효율을 제공한다.
- KFCT-8500 : 고밀도 및 저밀도 층, 얇은 박막, 광학 박막 및 전자기기 산업에서 사용되는 다층 박막 등을 증착 할 수 있다. 이 장비는 대형 유리판이나 금속 시트, 반도체 웨이퍼 등 대형 기판에도 적용 가능하다.
- KFCT-9000 : 고성능 자기제어 Sputtering 기술을 사용하여 높은 층 결합 강도, 좋은 표면 처리 특성 및 높은 생 산성을 제공한다.
(2) Applied Materials(AMAT)_해외
: 고성능 층을 만들기 위한 광범위한 공정 조건을 제공하며 높은 생산성과 고부가가치 층의 일괄 처리를 가능케 한다. 또한 다양한 소재, 크기 및 형상의 웨이퍼 및 서브스트레이트에 대한 고유한 공정 조건을 제공하는데 유연성이 있으며 고도의 자동화 및 프로세스 제어를 가능하게 한다.
[장비]
- Centura Sputter : 대형 원판형 타깃을 사용하여 반도체, 평판 디스플레이, 데이터 저장 매체 등의 공정에서 주 로 사용된다.
- Endura Sputter : 이 장비는 200mm, 300mm, 450mm 웨이퍼를 처리할 수 있으며, 다양한 애플리케이션에 사 용된다. Endura Sputter는 Ti, TiN, Al, AlCu, AlSi, W, WN 등의 다양한 금속 및 금속화합물을 코팅할 수 있 다. 이 장비는 주로 반도체 산업에서 전자기기 및 태양전지 패널 등의 생산에 사용된다.
▶3. CVD Intrepid
(1) Interpid
:Intrepid는 ASM International에서 개발한 CVD (Chemical Vapor Deposition) 장비 중 하나이다. 이 장비는 고객의 요구에 따라 광범위한 형태, 두께, 물성 및 재질 선택을 위한 유연성과 함께 고도의 생산성과 성능을 제공한다.
Intrepid는 자동화된 기술과 고성능 밸브, 펌프, 가열시스템 등의 혁신적인 기술이 결합되어 있다. 이를 통해 고객은 다양한 칩 및 부품 제작 과정에서 원하는 형태와 두께, 물성 및 재질을 선택할 수 있다.
또한 Intrepid는 고객의 요구에 맞게 조절 가능한 반응 챔버를 사용하여 광범위한 공정 조건을 처리할 수 있다. 이를 통해 고객은 다양한 응용 분야에 적합한 고성능 박막을 생성할 수 있다.
2) Interpid의 일반적인 구성
① Chamber (CVD Reactor)
최대 4개의 CVD 반응기 챔버를 지원한다. 각 챔버는 8인치, 12인치 또는 15인치 직경의 웨이퍼를 처리할 수 있다.
Chamber는 Dual Chamber, Tri Chamber, Quad Chamber 옵션으로 선택할 수 있다.
② Gas Delivery System
Gas Delivery System은 챔버 내부에 필요한 반응 기체를 공급한다. 다양한 가스 유량과 진공 요구 사항을 충족하는 다양한 Gas Panel 옵션을 선택 가능하다.
③ Heater
Intrepid 장비는 직접 가열 또는 인덕션 가열의 옵션을 선택할 수 있다. 각 챔버는 독립적으로 가열할 수 있으며, 고온 히터는 최대 1200도까지 가열이 가능하다.
④ RF & Microwave Plasma Systems
다양한 반응조건을 조절하며, 고체, 액체 또는 기체 상태에서의 프로세스를 제어할 수 있다. Plasma Sources는 다양한 종류와 크기로 제공되며, 사용자의 특정 애플리케이션에 맞게 선택할 수 있다.
⑤ Automation
Intrepid 장비는 자동화 시스템을 통해 고부가가치 웨이퍼 처리를 수행한다. 고객은 SECS/GEM과 같은 다양한 인터페이스를 사용하여 생산 공정을 관리할 수 있다.
⑥ Advanced Process Control
공정에서 발생하는 여러 가지 변수를 모니터링하고 제어하여 공정 안정성과 제품 품질을 향상한다.
(3) 동작과정
①로딩: 원료를 로딩할 수 있는 샘플 하나를 수용할 수 있다. 로딩이 완료되면 로딩 포트가 밀봉된다.
②진공 펌핑: 로딩이 완료된 후에는 시스템 내부의 대기압을 제거하기 위해 진공 펌핑이 이뤄진다.
③ 전구 가열: 샘플이 위치한 샘플 홀 주변의 전구를 가열하여 시스템 내부 온도를 증가시킨다.
④전구 위치 조정: 전구 위치는 샘플과의 거리를 조절하여 필요한 CVD 반응이 일어날 수 있도록 한다.
⑤선행 처리: 샘플에 대해 선행 처리가 이루어질 수 있다. 이는 샘플의 표면을 깨끗하게 유지하고, CVD 반응에 필요한 적절한 표면을 형성하기 위해 수행된다.
⑥기체 공급: CVD 공정에 필요한 기체가 샘플에 공급된다. 이 기체는 샘플의 표면과 반응하여 특정한 증착 층을 형성한다.
⑦반응 시간: 샘플에 기체가 공급되는 동안, 적절한 반응 시간을 유지한다. 이를 통해 원하는 증착 층이 샘플에 형성된다.
⑧기체 제거: CVD 반응이 완료된 후, 기체는 시스템에서 제거된다.
⑨후처리: CVD 공정 후, 생성된 증착 층을 적절하게 처리한다. 후처리에는 열처리, 냉각 처리, 산화 처리 등이 포함될 수 있다.
⑩언로딩: 샘플이 공정을 완료하면, 샘플은 시스템에서 언로드 된다.
▶4. Centura Sputter
(1) Centura Sputter
: Centura Sputter는 고객의 요구에 따라 다양한 기술적 규격을 가진 모델을 제공한다. 예를 들어, Centura Sputter는 고밀도 증착 (HDP) 공정을 지원하는 HDP-CVD 적층기능을 갖추고 있으며, 고속 증착 기능 (High-speed Deposition)을 지원하는 SuperFill 기술도 사용할 수 있다. 이 장비는 실리콘, 금속, 산화물 및 질화물 같은 다양한 재료를 증착할 수 있다.
또한, Centura Sputter는 기판의 크기와 형태에 대해 유연하게 대응할 수 있는 기술을 갖추고 있다. 300mm 웨이퍼까지 대응 가능하다.
(2) 구성
① Load Lock Chamber: 원료 또는 샘플 웨이퍼를 적재하거나 반출할 때 사용된다.
② Transfer Chamber: LoadLock Chamber와 Main Process Chamber 사이 샘플전송 역할을 한다.
③ Main Process Chamber: Sputtering 프로세스가 수행되는 핵심 챔버이다. 이 곳에서 증발된 타겟 소재로부터 입자들이 생성되고, 원하는 두께 및 특성을 갖는 박막이 웨이퍼 위에 적층된다.
④ Cryo Pump: 고성능 열 제거를 위해 액체 진공 유체를 사용하여 매우 높은 진공 수준을 유지한다.
⑤ Turbo Pump: 높은 진공을 유지하는 데 필요한 고속 회전으로 가스 분자를 펌핑한다.
⑥ RF Power Supply: RF 전원 공급 장치로서, 웨이퍼 위의 샘플과 함께 작동한다.
⑦ Target: 원자층 증발에 사용되는 소재이다. 주로 금속 또는 금속 합금으로 구성되며, 증발 및 입자 생성 과정에서 소모된다.
⑧ Wafer Chuck: 웨이퍼를 챔버 내에 고정시키는 장치이다. RF 전원을 통해 웨이퍼 위의 타겟 입자를 가속시켜 박막 적층 과정을 수행한다.
⑨ Gas Inlet: Sputtering 프로세스에 필요한 가스를 제공한다. 적절한 비율과 압력으로 혼합하여 챔버 내에 공급되어 입자 생성 및 적층에 필요한 적정 환경을 조성한다.
⑩ Optical Endpoint Detector: 박막 적층 과정에서 사용되며, 현재 박막 두께를 실시간으로 모니터링 한다. 정확한 층 두께를 측정하여 종료 시점을 결정하는 데 사용된다.
⑪ Control System: Sputtering 공정을 제어하기 위한 제어 장치로, 고도로 자동화된 공정 제어를 제 공한다. 이는 공정의 일관성과 안정성을 보장한다.
3) 동작과정
① 로드락 챔버에서 표적판을 로드락 챔버의 열린 포트를 통해 이송한다.
② 표적판이 이송되면, Pre-clean 공정으로 표적판 표면을 청소한다. 이 과정에서 고주파 RF파워를 사용하여 표적판 표면의 불순물과 산화물을 제거한다.
③ Pre-clean 후, 표적판은 Transfer Chamber로 이동된다.
④ Transfer Chamber에서 표적판은 마스크를 사용하여 원하는 패턴으로 마스킹되며, 이 마스크는 공 정에서 부식되지 않는 재질로 만들어진다.
⑤ 마스킹된 표적판은 다시 로드락 챔버로 이송된다.
⑥ 로드락 챔버에서 스퍼터링 타깃(Target)을 이온화시킨다. 이온화된 입자는 고전압에서 에너지를 획득 하면서 표적판으로 향한다.
⑦ 이온화된 입자는 표적판 표면에 충돌하면서 스퍼터링 현상을 일으키고, 이렇게 방출된 입자들이 표적 판의 원자와 이온으로 구성된 층을 형성한다.
⑧ 표적판은 다시 Transfer Chamber로 이동된다.
⑨ Transfer Chamber에서, 표적판은 다시 공정 전처리를 위해 Pre-clean 공정으로 이동한다.
⑩ 표적판은 다시 로드락 챔버로 이동되어 새로운 패턴으로 마스킹되고, 다시 스퍼터링을 진행한다.
⑪ 공정이 끝나면, 로드락 챔버의 열린 포트를 통해 표적판이 제거된다.
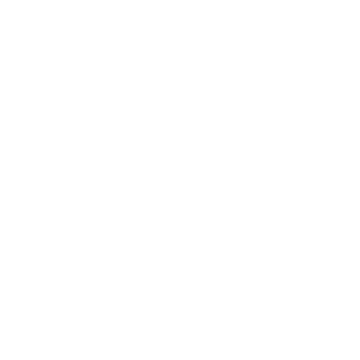
'Semiconductor > Semiconductor Fabrication' 카테고리의 다른 글
[반도체 공정] Moore's Law & Huang's Law (무어의 법칙 & 황의 법칙) (0) | 2024.05.15 |
---|---|
[반도체 공정] 플라즈마 공정, 플라즈마 장비 (0) | 2024.05.15 |
[반도체 공정] 이온 주입 공정, 이온 주입 장비 (0) | 2024.05.14 |
[반도체 공정] 패키징 공정, 패키징 장비 (0) | 2024.05.14 |
[반도체 공정] 웨이퍼 제조, 웨이퍼 제조 장비 (0) | 2024.05.07 |
전자공학 블로그에 오신 것을 환영합니다! 최신 기술 동향, 회로 설계, 반도체 및 전자 부품에 대한 유용한 정보와 실습 팁을 제공합니다.