![[반도체 공정] 웨이퍼 제조, 웨이퍼 제조 장비](https://img1.daumcdn.net/thumb/R750x0/?scode=mtistory2&fname=https%3A%2F%2Fblog.kakaocdn.net%2Fdn%2Fbsvh41%2FbtsHb4UuFOD%2FAwy1wYQbAuEIX9zqucJHnk%2Fimg.png)
안녕하세요 이번 포스트부터 시작해서 반도체 공정에 대한 각 챕터별 공정 방식과 제조 장비에 대해 알아보겠습니다. 이번 글에서는 반도체의 가장 기반이 되는 웨이퍼에 대해 알아보겠습니다.
아래는 다양한 다른 반도체 공정 과정과 장비를 설명 드리고 있습니다. 참고해보세요.
0.반도체 8대 공정
https://semicircuit.tistory.com/144
1.웨이퍼 제조, 웨이퍼 제조 장비
https://semicircuit.tistory.com/17
2. 박막 공정, 박막 공정 장비
https://semicircuit.tistory.com/48
3. 패키징 공정, 패키징 장비
https://semicircuit.tistory.com/52
4. 이온 주입 공정, 이온 주입 장비
https://semicircuit.tistory.com/53
5. 플라즈마 공정, 플라즈마 장비
https://semicircuit.tistory.com/54
6. 노광 공정, 노광 장비
https://semicircuit.tistory.com/57
7. 세정 공정, 세정 장비
https://semicircuit.tistory.com/59
8. 식각 공정, 식각 장비
https://semicircuit.tistory.com/60
※1. 웨이퍼의 제조기술
▶1. 웨이퍼
반도체 웨이퍼는 반도체 소자를 제조하는데 사용되는 기본 소재입니다.. 웨이퍼 위에 여러 가지 공정을 통해 반도체 소자를 형성하게 되는데, 이는 다양한 전자기기를 제조하는데 필수적인 과정입니다.. 반도체 웨이퍼를 이용하여 제조된 반도체 소자는 다양한 전자기기에 사용됩니다. 예를 들어, 컴퓨터, 스마트폰, 태블릿, 카메라, TV 등 다양한 전자기기에서 사용되는 반도체 소자들이 웨이퍼에서 만들어지게 됩니다.
웨이퍼의 전기적 특성은 단결정으로 성장시킨 웨이퍼 불순물의 첨가량에 따라 전기 전도율을 조절할 수 있음을 설명하며, 결정 특성은 순도 및 결정성에 따라 기계적 성질, 확산, 식각 특성에 영향을 끼친다. 가공특성은 반도체 소자 회로 제조 시 치명적인 영향을 주는 결함, 휨, 불순물 주일 균일도에 따른 비저항 분포 특성이 있다.
▶2. 공정 파라미터
▶3. 도핑(Doping)
도핑은 반도체 소자의 전기적 특성을 조절하기 위해, 반도체 소재에 의도적으로 작은 양의 불순물을 첨가하는 과정이다. 반도체 소재에 도핑 된 불순물은 원자 구조상으로 반도체 소재에 존재하는 원자와 다르게 전자 수가 많거나 적어져서, 반도체 소자의 전기적 특성을 바꿀 수 있다. N형 도핑은 반도체 소자에 비교적 많은 수의 자유 전자를 만들어내는데, 이로 인해 전기적으로 음(-)의 전하를 띄게 된다. P형 도핑은 반대로, 반도체 소자에 전자를 적게 만들어내고 대신 전자가 부족한 상태에서 양(+)의 전하를 띄게 된다. P형 도핑 된 반도체 소자는 전자의 이동성이 낮아져서, 전기적으로는 양(+) 극에 연결되어 있는 전자를 쉽게 이용할 수 있다.
▶4. 형태에 따른 웨이퍼 종류
① SOI(Silicon On Insulator) 웨이퍼
: Si 웨이퍼 사이에 SiO2(Silicon Dioxide)와 같은 절연 박막을 삽입시킨 형태로 웨이퍼 접합(bonding) 기술이 어렵지만 고온, 소비전력 및 응답속도 특성이 기존 Si 웨이퍼에 비해 우수하다.
② 에피(Epi 또는 Epitaxial) 웨이퍼
: 동일한 결정구조를 가지는 고품질의 단결정 층을 성장시킨 웨이퍼로서 표면 결함이 적고 불순물 제어가 용이하여 우수한 구조적, 전기적 특성을 나타낸다.
※2. 단결정(Single Crystalline) Si 웨이퍼 제조기술
: 잉곳의 목적은 고순도의 실리콘 원료를 얻기 위함이다. 실리콘 원료는 반도체 소자를 제조하는 데 매우 중요한 재료이다. 그러나 실리콘 원료는 순도가 낮을 경우 반도체 소자의 성능을 저하시키는 요인 중 하나이다. 따라서 고순도의 실리콘 원료가 필요하다. 이를 위해 잉곳 제조 과정에서는 순도를 높이기 위해 다양한 기술이 사용된다.
▶1. 단결정 Si 잉곳 제조 방법 및 특성
① 초크랄스키(Czochralski, CZ) 방법
: 쵸크랄스키 공정(Chochralski method)은 반도체 산업에서 가장 널리 사용되는 실리콘 잉곳 제조 공정 중 하나이다. 고순도의 실리콘 원료를 용융시켜 잉곳을 성장시키는 방식으로 이루어진다.
② 브리지만(Bridgman) 방법
: 브리지만 공정에서는 용융된 실리콘 원료를 각종 결정 방해 요소 없는 용기에 담아두고, 용기를 천천히 회전시키면서 원료를 냉각시킨다. 이 과정에서는 냉각 과정이 매우 느리게 이루어져 실리콘 결정이 천천히 성장되며, 이를 통해 고순도의 실리콘 잉곳을 생산할 수 있다.
③ 부유대용융(Floating Zone, FZ: 플랫존) 방법
: 실리콘 결정을 고온에서 용융시켜 결함을 제거하고 순도를 높이는 공정이다. 이 공정은 산화막 반도체 제조에서도 사용된다. 플랫존 방법은 일반적으로 샘플을 용융하고 녹인 샘플을 단열체에 옮겨놓고 천천히 움직여 일정한 속도로 냉각시키는 과정으로 이루어진다. 이를 통해 고순도의 실리콘 웨이퍼를 제조할 수 있다.
▶2. 웨이퍼링(Wafering) 공정
웨이퍼 fab(팹) 공정은 반도체 제조 과정에서 웨이퍼를 대량으로 생산하기 위해 사용되는 공정이다. "Fab"은 "팹리케이션(fabrication)"의 줄임말로, 반도체 제조 공정을 의미한다.
: 웨이퍼링 공정은 반도체 제조 과정 중 일부로, 실리콘 웨이퍼(반도체의 기판)를 특정 두께로 연마하고 평활화하는 공정이다. 반도체 제조에서 웨이퍼는 전기적 신호를 전달하는 기본 부품으로 사용되기 때문에 반도체 제조 과정 중에서 가장 중요한 단계 중 하나이다.
<과정>
① 잉곳 고정(잉곳 지지) - 웨이퍼를 잉곳으로 고정
: 잉곳을 에폭시로 작업대 위에 접착시켜 절단 시 발생할 수 있는 edge chipping(또는 crack)을 방지하고 웨이퍼가 정확한 결정 방향을 가질 수 있게 한다.
② 와이어 소잉(Wire Sawing,Slicing:절단) - 와이어 소(Saw)를 이용하여 웨이퍼를 절단
: 다이아몬드 블레이드 또는 다이아몬드 와이어(일종의 줄톱)를 이용하여 절단하는데 와이어 장력을 동일하게 유지하기 위해 자동 장력 제어기(auto tensioner)를 사용한다.
③ 연삭(Edge Grinding) - 웨이퍼의 엣지를 연마하는 공정
: 이후 공정에서 웨이퍼 bevel 부분의 취약성에 따라 칩핑(Chipping), 깨짐(broken) 문제를 방지하고 불순물을 제거 및 깨끗한 표면을 만드는 공정으로 반도체 소자 제조공정 시 결함 발생을 최소화할 목적으로 모서리 연마를 한다.
④ 레이저 마킹(Laser Marking) 및 분류(Sorting) - 레이저를 이용하여 마킹 및 품질 분류
: 레이저 마킹은 웨이퍼의 두께 분류 및 lot관리를 위해 레이저 마킹 공정을 진행한다. 레이저를 사용하여 부호, 식별 정보 및 패턴을 마킹하는 과정으로 이 과정은 웨이퍼를 식별하고 추적하기 위해 사용된다. 웨이퍼 표면에 접촉 없이 레이저를 이용해 부호를 새기기 때문에 웨이퍼 표면을 손상시키지 않는다. 분류 공정은 웨이퍼의 두께를 자동으로 분류하는 공정이다.
⑤ 랩핑(Lapping) - 웨이퍼 표면을 평활하게 연마하는 공정
: 슬러리(Slurry)를 웨이퍼 위에 공급하고 웨이퍼 양면의 표면을 가공하여 웨이퍼 표면의 평탄도 편차를 크게 감소시킨다. 이후 연마(Polishing) 공정을 이용한 두께 및 표면품질 제어를 용이하게 한다.
⑥ 식각(Etching) - 웨이퍼 표면을 식각액으로 처리하여 불순물을 제거하는 공정
: 와이어 소잉, 연삭 및 랩핑 공정에서 발생하는 다양한 깊이의 damage layer(saw mark, macro crack, micro crack, stress)를 물리적으로 제거하기 위한 식각 공정이며, damage later를 제거하기 위해 여러 가지 식각제(etchant)를 사용한다.
⑦ 열 처리(Heat Treatment) - 웨이퍼를 고온 처리하여 비저항 안정화, 마이크로 응력 제거
: 실리콘웨이퍼 결정에서 산소가 불순물로 잔존하여 일정 온도에서 donor화가 진행되어 웨이퍼 및 소자 비저항 증가의 원인으로 작용하는데 이를 제거하기 위해서는 N2와 같은 불활성 가스를 포함하는 대기에서 600~700도의 온도로 20~30분간 열처리한다.
(와이어 소잉 또는 슬라이싱 공정 중 웨이퍼 표면의 마크로 크랙(macro crack)하부에는 마이크로 응력이 존재하는데, 응력은 소자 패키지 단계의 다이싱(dicing) 공정 중 칩 깨짐(chip broken)의 원인으로 작용할 수 있다. 이를 제거하기 위해 열 처리가 필요하다.)
⑧ 지지 또는 고정(Wax Mounting) - 웨이퍼를 왁스로 고정하는 공정
: 웨이퍼를 왁스로 고정하여 다른 공정에서 사용할 수 있도록 하는 공정으로 웨이퍼를 세라믹 판에 고체 왁스(Solid wax, 80~100도 용융점)를 이용, 고정한다.
⑨ 연마(Polishing) - 웨이퍼 표면을 연마하여 불순물을 제거하고 깨끗한 표면을 만드는 공정
: 웨이퍼 표면을 슬러리 내 함유된 수용액과 연마제로 화학적, 기계적 연마함으로써 반도체 소자 배선 선폭 수준의 경면을 확보하며 표면을 먼지, 오염 및 불순물로부터 제거하고, 반도체 소자 제작에 필요한 정확한 두께와 표면 특성을 얻기 위해 수행된다.
⑩ 세정(Cleaning) - 웨이퍼를 청소하여 불순물과 오염을 제거하는 공정
: 웨이퍼 표면에 잔류하는 particle, native oxide(자연 산화막) 및 금속 불순물(특히 galvanic corrosion을 발생시켜 Si 결정 경함을 유발하는 Cu 이온) 제거를 위해 batch tpye의 Wet Station 장비 또는 Single 웨이퍼 cleaning 장비에서 화학 약품을 이용한다.
⑪ 검사(Inspection) - 웨이퍼의 품질을 검사하여 불량품을 제거하는 공정
: nano-topography(나노 스케일의 표면 분석), 평탄도 및 particle 특성을 검사하며, 표층 특성에 영향을 끼치는 결정 결합, 금속 불순물 및 강도 등을 측정한 다음, 품질 수준에 따라 웨이퍼 등급을 분류한다.
⑫ 포장(Packing) - 웨이퍼를 포장하여 출하 준비하는 공정
: 웨이퍼를 안전하게 포장하는 단계로 웨이퍼를 보관하는 카세트(Cassette)와 카세트를 보호하기 위한 정전 방지 비닐 및 알루미늄을 2중 진공포장하고 종이 박스 여러 카세트를 넣어 포장을 완료한다.
※3. 다결정(Poly Crystalline) Si 웨이퍼 제조기술
: 다결정 Si 웨이퍼는 단결정 Si 웨이퍼에 비해 공정이 간단하고, 가격도 저렴하지만 전력 변화 효율이 낮아 단결정 SI 웨이퍼에 비해 사용이 적다.
▶1. 다결정 Si 잉곳 제조 방법 및 특성
① DS(Directed Solidification) 방법 : 하나의 도가니에서 잉곳의 양을 줄이는 데 매우 효과적이지만, 비용이 높고 제한된 크기의 결정만 사용할 수 있어 대량 생산에는 적합하지 않다.
② Cast 방법 : 하나의 도가니에서 용융한 후, 별개의 도가니에 부어 방향성 응고시키는 방법으로 DS 방법보다 비용이 적게 들고 대량 생산이 가능하다. 그러나, 결정 내부에서 생길 수 있는 잉곳이 많아 고순도의 웨이퍼 생산에는 적합하지 않다.
③ EMC(Epitaxial Mono Crystal) 방법 : 유도가열방식에 의해 설계된 금속 도가니를 사용하여 Si가 도가니 벽과 접촉하지 않도록 고안된 기술로 반 연속적으로 응고된 Si 잉곳을 추출한다. 고순도의 웨이퍼를 생산할 수 있으며, 반도체 재료로 사용되는 웨이퍼의 품질을 향상시키지만 DS나 Cast 방법에 비해 높은 비용과 생산성이 떨어지는 단점이 있다.
※4. 사파이어(Sapphire) 웨이퍼 제조기술
: 사파이어 웨이퍼는 LED 용 웨이퍼, 렌즈 커버, 홈 센서 커버 등으로 사용되는데, 극저온, 초고온에서 안정적이며, 또한 우수한 기계적 성질과 다이아몬드 다음으로 높은 경도를 가지고 있어 산 알칼리 화학약품에 내화학성이 높다. 또한 빛의 투과성, 열전도도, 유전율 상수 및 비저항이 높은 소재이다.
▶1. 사파이어 잉곳 제조 방법 및 특성
① Kyropoulos 공법: CZ 공법을 응용한 공정으로 용액에 씨드를 넣고 온도를 천천히 하강시킴과 동시에 결정을 위로 올리며 잉곳을 제조한다. 대형 사파이어 웨이퍼 생산에 적합하다.
② CZ 공법: 도가니에 원료를 용해한 다음 단결정 씨드를 접촉한 후 회전하면서 서서히 끌어올려 결정을 성장시킨다. 실리콘 웨이퍼 제조에 많이 사용되는 방법으로, 사파이어의 순도를 높일 수 있어 광학 재료로서의 용도에 적합하다.
③ VHGF(수직 수평 온도구배) 공법: 단결정이 육면체 도가니 안에서 천천히 응고하면서 성장시켜 잉곳을 제조한다. 다양한 크기의 사파이어 웨이퍼를 생산할 수 있어 산업적으로 유용하다.
※5. 단결정(Mono Crystalline) Si 웨이퍼 제조 장비 기술
▶1. Si 잉곳 성장 장비(CZ) 구성 및 운영 시스템
Czochralski 성장 방식에서 중요 인자는 결정 성장 속도(V)와 고액 계면에서의 온도구배(G)의 비율인 V/G이며, V/G를 결정성장의 전 구간에 걸쳐 설정된 목표 궤적 값으로 제어하는 것이 중요하다.
CZ 공법에 의한 제어시스템은 기본적으로 현재 직경 모니터링 시스템에서 읽은 변화량과 PID 제어부(Controller)를 통한 연산으로 target의 pulling 속도를 맞추기 위한 실제의 인상 속도를 변화시키는 모터 동작부터 구성된다.
잉곳 성장 장비 제어를 위한 소프트웨어에는 기본적으로 모션, 진공 압력, 온도, 가스 유량 등의 공정제어부가 있으며, GUI 화면에는 공정 및 장비 상태를 파악할 수 있다.
▶2. Si 잉곳 성장의 단위공정별 장비 파라미터
: 각 단계에서 적절한 파라미터를 설정하여 높은 품질과 생산성을 확보할 수 있다. 이에 따라 파라미터 설정에 대한 연구와 최적화가 중요하다.
▶3. CZ 장비에서 주요 모듈의 핵심 요소 기술
(1) 와이어 소잉 장비
① 장력 제어부(tension control)
: 장력 측정 및 제어를 하는 자동 장력 롤러를 구성한다.
② 잉곳 고정부(Mounting)
: Si 잉곳(Block)을 고정 및 와이어에 피딩 한다.
③ 와이어 소잉 Method
: 웨이퍼 표면 품질을 향상시키기 위한 소잉 메커니즘을 통해 절단면의 균일도를 향상시킬 수 있다.
④ 와이어 구조
: 웨이퍼 표면 품질 향상을 위한 와이어 구조인 fixed abrasive type wire를 이용한 소잉 기술은 기존의 절단면 넓이가 크기 때문에 발생하는 낮은 웨이퍼 수율, 연삭 잔류물에 의한 세정 공정의 어려움을 해결해 줄 수 있다.
(2) 연삭(Edge Griding) 공정 장비
① 웨이퍼 정렬 기술: 연삭 공정에서 웨이퍼의 정확한 위치 조정은 매우 중요하다. 일반적으로 레이저나 카메라를 사용하여 웨이퍼의 위치를 감지하고, 로봇 암 등을 이용하여 정확한 위치 조정을 수행한다.
② 스핀들(spindle) 구동 기술: 연삭 공정에서는 스핀들이 웨이퍼의 가장자리를 연삭하는데 사용된다. 스핀들은 고속 회전하는 원반 형태로, 다양한 소재의 연마 휠을 장착하여 사용된다.
③ 세정 방식: 연삭 공정 후 웨이퍼의 표면에 묻어난 연마 먼지와 기타 불순물을 제거하기 위해 세정 공정이 수행된다. 이를 위해 산화알루미늄, 황산 등의 산성 또는 염기성 용액을 사용하거나, 플라즈마 처리 등의 고급 세정 방식을 채택하기도 한다.
④ 웨이퍼 지름 및 두께 측정 장치: 연삭 공정에서는 웨이퍼의 지름과 두께가 정확해야 한다. 이를 위해 레이저나 카메라 등을 사용하여 웨이퍼의 지름과 두께를 측정하는 장치를 사용하다. 이런 측정 장치는 공정의 효율성을 높이고 제품의 품질을 유지하기 위해 매우 중요하다.
(3) 기계적 연마(Lapping) 장비
① 상하 부판(upper/ lower plate)부: 다공성 연마 패드가 부착되어 있다.
② 가압(Pressure) 부 : 상정반에 압력을 가하기 위한 모듈
③ 이송부(Carrier or template) 부 : 다수의 웨이퍼를 고정 시 킨다.
④ 연마 슬러리(Slurry) 공급부
⑤ 슬러리 저장부: 연마 잔류물(Polishing residures) 회수 및 배출시킨다.
(4) 연마(Polishing) 장비
① 웨이퍼 정렬 시스템: 연마 공정에서는 웨이퍼의 정확한 위치 조정이 필요하다. 따라서 웨이퍼 정렬 시스템은 웨이퍼의 위치를 감지하고 조정하기 위한 카메라, 레이저 및 로봇 암 등의 장치를 포함한다.
② 연마 패드(Polishing pad): 연마 패드는 웨이퍼와 접촉하여 연마 작업을 수행한다. 보통 연마 패드는 폴리우레탄 재질로 만들어지며, 패드의 경도와 표면 특성은 연마 공정의 결과에 영향을 미친다.
③ 연마 헤드(Polishing head): 연마 헤드는 연마 패드를 움직여 웨이퍼의 표면을 연마한다. 보통 연마 헤드는 자동으로 움직이는 로봇 암 형태로 되어 있다.
④ 슬러리 공급 시스템(Slurry delivery system): 연마 시에는 웨이퍼와 연마 패드 사이에 슬러리라는 연마 용액을 공급한다. 이를 위해 슬러리 공급 시스템은 슬러리를 혼합하고 공급하는 장치와, 슬러리의 온도, 압력 등을 제어하기 위한 제어 장치를 포함한다.
⑤ 측정 장치: 연마 공정 후 웨이퍼의 표면 특성을 측정하는 장치를 포함한다. 보통 표면 거칠기, 평평도, 박리 등의 특성을 측정하며, 이를 통해 연마 공정의 효율성과 웨이퍼의 품질을 평가한다.
⑥ 제어 시스템: 연마 공정은 다양한 변수에 영향을 받기 때문에 정밀한 제어가 필요하다. 따라서 제어 시스템은 연마 공정의 다양한 변수를 제어하며, 안정성과 반복성을 보장한다.
(5) 품질검사 장비
① 웨이퍼 제조 단위 공정별 물리적 특성 : 웨이퍼 제조 단위 공정, 슬라이싱(소잉), 식각 및 연마 기술 이후, 물리적 특성은 평탄도, Nano-topography 및 조도(혹은 거칠기)로 표현할 수 있다.
② 화학적 물성 시험분석 항목 및 장비 : ICP-MS, WOS-GCMS, SEM-EDS, TXRF, Dynamic-SIMS 등이 웨이퍼 표면과 내부의 산화막 내 금속 농도, 유기물 농도, 유기물 농도, 파티클 성분, 금속 오염 농도, 모바일 이온 농도 등으로 측정한다.
이상으로 웨이퍼란 무엇이고 웨이퍼를 제조하는 장비는 어떻게 구성되고 동작하는지에 대한 포스트를 마치겠습니다. 앞으로도 여러 공정과 장비에 대해 작성하겠습니다. 감사합니다.
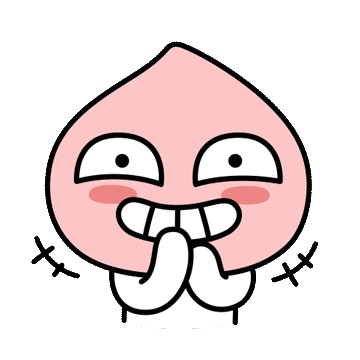
'Semiconductor > Semiconductor Fabrication' 카테고리의 다른 글
[반도체 공정] Moore's Law & Huang's Law (무어의 법칙 & 황의 법칙) (0) | 2024.05.15 |
---|---|
[반도체 공정] 플라즈마 공정, 플라즈마 장비 (0) | 2024.05.15 |
[반도체 공정] 이온 주입 공정, 이온 주입 장비 (0) | 2024.05.14 |
[반도체 공정] 패키징 공정, 패키징 장비 (0) | 2024.05.14 |
[반도체 공정] 박막 공정, 박막 공정 장비 (0) | 2024.05.13 |
전자공학 블로그에 오신 것을 환영합니다! 최신 기술 동향, 회로 설계, 반도체 및 전자 부품에 대한 유용한 정보와 실습 팁을 제공합니다.