![[반도체 공정] 이온 주입 공정, 이온 주입 장비](https://img1.daumcdn.net/thumb/R750x0/?scode=mtistory2&fname=https%3A%2F%2Fblog.kakaocdn.net%2Fdn%2FcckysS%2FbtsHmBSxnBc%2FfzvkHwHhWEzESNOCCOlC00%2Fimg.png)
안녕하세요.
반도체 이온주입 공정은 반도체 소자의 전기적 특성을 조절하고, 저항 및 전하 이동 특성을 개선하여 반도체 소자의 성능을 향상시키는 핵심적인 단계입니다. 이는 고성능 및 저전력 전자 기기의 제조에 필수적입니다.
아래는 다양한 다른 반도체 공정 과정과 장비를 설명 드리고 있습니다. 참고해보세요.
0.반도체 8대 공정
https://semicircuit.tistory.com/144
1.웨이퍼 제조, 웨이퍼 제조 장비
https://semicircuit.tistory.com/17
2. 박막 공정, 박막 공정 장비
https://semicircuit.tistory.com/48
3. 패키징 공정, 패키징 장비
https://semicircuit.tistory.com/52
4. 이온 주입 공정, 이온 주입 장비
https://semicircuit.tistory.com/53
5. 플라즈마 공정, 플라즈마 장비
https://semicircuit.tistory.com/54
6. 노광 공정, 노광 장비
https://semicircuit.tistory.com/57
7. 세정 공정, 세정 장비
https://semicircuit.tistory.com/59
8. 식각 공정, 식각 장비
https://semicircuit.tistory.com/60
※1. 확산(Diffusion) 공정장비
▶1. 확산(Diffusion)
반도체 공정에서의 확산은 고온에서 이온이나 원자가 반도체 내부에서 이동하여 농도를 조절하는 과정으로, 반도체 소자의 전기적 특성을 제어하는 중요한 공정이다. 이 과정은 도핑이나 적층 형성에 이용된다. 대표적으로 확산 방법으로 석영 튜브를 장착한 확산로(furnace)에 웨이퍼를 위치시킨 다음, 불순물이 포함된 가스를 주입시키고, 전기로를 가열하여 고온으로 확산로 내부를 일정시간동안 유지하면 웨이퍼 내부에 불순물이 확산되어 도체를 형성한다. 확산은 물질의 상태에 관계없이 노동 차에 의한 물질이동현상을 이용하여 이온주입에 의한 source/drain well PN 및 junction 형성, annealing에 의한 불순물(dopant)의 확산, silicon 기판에 고온의 산소(O2) 주입에 의한 산화막(Silicon Dioxide) 성장 및 고온 quartz에서 공정 가스의 화학반응에 의한 박막 증착 공정에 응용되고 있다. 확산공정에서는 농도 구배, 온도, 공정시간, 격자결함, 확산정도(Diffusivity) 및 확산계수(Diffusion Coefficient) 등의 공정 변수로 작용한다.
▶2. 확산(Diffusion) 기술 분류
① 이온주입(Ion implant) 기술 - 높은 에너지를 가지는 dopant를 웨이퍼에 주입하는 공정
: dopant를 웨이퍼에 주입하는 공정으로 Si에 전도성을 부여하거나, 전기적 특성을 향상시키기 위한공정으로 소자의 미세화, 고집적화에 따라 이온주입 공정 횟수가 증가하고 있다. 고온(800~1200도)에서 Si 내부로 B등과 같은 3족 불순물을 주입하면 P-형 반도체 영력이 형성되고, 5족 불순물인 P, As 등을 주입하면 N-형 반도체 영역이 형성된다.
② 열처리(Annealing) 기술 - 고온에서 반도체 소자를 가열하여 결함을 제거하거나 결정 구조를 정렬시키는 등의 목적으로 사용되는 공정
: 이온 주입된 dopant를 Si 내부로 확산시켜 P 또는 N type의 junction을 형성하고, 또한 주입된 dopant를 전기적으로 활성화시키며 이온 주입에 위해 손상된 Si 결정이나 불완전한 Si-dopant 결함(bond)이 안정되게 결정화되도록 한다. 주로 800~900도에서 진행한다. Gap-fill 절연막의 수분제거, 프로파일을 개선, 산화반응 억제, 접촉 저항 감소 불완전 결합의 회복, refresh 특성을 개선
③ 열산화막(Thermal Oxidation) 기술 - 고온과 산소를 이용하여 반도체 소자 표면에 산화막을 생성하는 공정
: 반도체 Si 웨이퍼가 대기 중에 노출되면 실리콘과 산소 간 반응으로 산화막을 형성하는 것을 응용한 기술로써 Si 기판에 고온의 산소를 주입하여 고순도 열 산화막을 성장시킬 수 있다. 일반적으로 800~1100도에서 고순도 산화막을 형성한다. 확산로에서 성장한 고온 산화막은 주변 불순물(오염원)을 차단하여 Si 표면 오염을 방지하고 비저항, 전도율을 안정화한다.
④ 화학증착(Chemical Vapor Deposition, 혹은 화학기상증착) 기술 - 기체 상태의 화학물질을 이용하여 반도체나 다른 고체 표면 위에 박막을 형성하는 기술이다.
: 확산로 장비에서 다양한 공정 gas를 주입하여 650도 이상의 온도에서 반응시킴으로써 고순도 박막을 형성하는 Rt의 스위치 역할을 하는 gate oxide, 소자에서 데이터 저장 및 읽기를 위해 capacitor insulator로 응용 된다.
▶3. 확산(Diffusion) vs 이온주입(Ion Implantation)기술
▶4. 이온주입(Ion Implantation)기술
(1) 공정변수
① Dopant : 이온주입에 사용되는 불순물
② Dose : 단위 면적당 웨이퍼에 주입되는 이온의 개수
③ Energy : 전압의 세기에 따라 이온이 가지는 가속된 힘
④ Beam Current : 단위 시간당 주입되는 불순물의 양을 전기적으로 표현한 값
⑤ Tilt/Twist(Beta/Alpha) : 웨이퍼를 implant beam을 기준으로 기울이거나 회전시키는 것
▶5. 열처리(Annealing)기술
(1) 열처리 온도에 따른 소자 특성 변화
① 450도 : 부분적 활성화, 부분적 손상회복
② 600도 : Epitaphial 막의 재 결정화, 비정질의 부분적 활성화
③ 900도 : 고농도 이온 주입의 활성화, 이동도(mobility)의 회복
④ 1000도 : 소수 carrier 수명의 회복
(2) 열처리(Annealing)기술
① 퓨너스(Furnace) 장비: 퓨너스는 반도체 소자에 고온 열처리를 적용하는 데 사용되는 장비이다. 소자를 미끄러지는 이송벨트 위에 올려놓은 후, 소자를 고온으로 가열하여 결함을 제거하거나 결정 구조를 정렬시키는 등의 역할을 한다. 이는 반도체 제조 과정에서 가장 기본적인 기술 중 하나이며, 대부분의 반도체 업체에서 사용하고 있다.
② RTP(Rapid Thermal Processing) 장비: RTP는 반도체 소자의 열처리를 훨씬 빠르게 수행할 수 있는 장비이다. 이는 반도체 소자에 짧은 시간 동안 높은 온도를 가할 수 있는데, 이것은 소자의 특정 특성을 개선하거나, 반도체 소자의 생산량을 높일 수 있다. RTP는 퓨너스보다 훨씬 더 높은 가열 속도와 더 높은 가열 온도를 제공하며, 일반적으로 반도체 소자의 특정 부분을 가열하거나, 소자 전체적으로 가열하는 데 사용된다.
▶6. 열 산화막(Thermal oxidation)기술
(1) 열 산화막 기술의 구분
① 건식 산화막 (Dry Oxidation) : 산소 기체(O2)를 사용하여 반도체 표면에 산화막을 생성하는 기술로, 높은 온도에서 수행된다.
② 습식 산화막 (Wet Oxidation) : 산화막 생성을 위해 산소 기체 대신 수증기(H2O)를 사용하는 기술로, 보다 낮은 온도에서 수행된다.
=> 건식 산화 기술의 공정은 단순하고 안전하지만 성장속도가 느리고 습식 산화 기술은 기화 발생기(vapor generator) 장치가 추가적으로 필요하지만 빠른 성장 속도를 가진다.
(2) 열 산화막 장비의 분류
① 산화막(Furnace Oxidation) 장비 : 일반적으로 사용하는 장비로 외벽에 위치하는 히터를 이용하여 다수의 웨이퍼 표면에 산화막을 성장시킬 수 있는 가열 방식이다.
② RTO(Rapid Thermal Oxidation) 장비 : 할로겐 램프 가열(Halogen Lamp Heating) 방식으로 1장의 웨이퍼에 산화막을 성장시키는 시킨다.
③ 플라즈마 산화막(Plasma Oxidation) 장비 : 진공 챔버에 산소를 주입하면서 O2 플라즈마를 발생시켜 실리콘과이 반응성을 증가시킨다.
▶7. 화학기상증착 기술
(1) 박막 종류 별 특성
① Nitride : 고밀도 절연막, 강한 stress, high-k, Passivation, Hard 마스크
② Poly Si : 고온 적합, doping으로 저항 조절 용이
③ TEOS : 640~680도, TEOS precursor 이용
④ MTO : 740도 공정, Gate Oxide 응용
⑤ HTO : 900도 공정, Capacitor 유전물질(insulator)
※2. 확산(Diffusion) 공정 장비기술
▶1. 이온 주입 장비
: 이온 주입 장비는 이온소스, 질량분석기, 이온가속기, 스캐닝 장치로 크게 4가지로 분류됨
① 이온소스(Ion Source, Arc Chamber) - 이온 생성 및 추출
: DC전원을 사용하여 텅스텐 재질의 Filament에 전류를 흘려주어 가열시키면 Hot Electron이 방출되고 원하는 Type의 이온이 포함된 Dopant Gas를 Chamber에 주입하면, Hot Electron이 Dopant Gas와 충돌하면서 양이온은 형성한다. 이때, 양이온 뿐만 아니라 전자, 핵, 중성자 4가지가 형성되는데 그 중 원하는 양이온을 추출하기 위해서 25[kv] 고전압을 인가해주면 전체가 양극이 되기 때문에 양이온만 추출가능하다.
② 질량분석기(Ion analyzer magnet) - 이온 질량 분석을 통해 이온 선택
: Ion Source부에서 생성된 이온이 일정 에너지를 가지고 나오게 되면 Magnetic Field(자기장)를 인가해줌으로써 양이온이 Path를 따라 이동하다가 E-field에 의해서 선택적으로 작은 질량의 가벼운 이온은 빠르게 꺾이고, 무거운 질량의 이온은 천천히 꺾이는 특성을 이용하여 원하는 양이온을 선택적으로 추출할 수 있다.
③ 가속기(Accelerator) - 이온에 추가적인 에너지를 주어 이온을 가속화
: 조리개(Resolving Aperture)를 통해 빠져나온 선택된 이온이 가속부에서 E-field에 의해 에너지가 추가적으로 이온에 가해진다. 양이온에 DC 마이너스 전원 방량으로 끌리는 원리를 이용하여 원하는 수준으로 가속할 수 있다. 필요한 정도에 따라 1[KeV]~수십[MeV] 단위까지 가속 시킬 수 있다.
④ 빔 가이드 및 스캐너 - 웨이퍼에 정해진 Dopant를 균일한 양으로 이온 주입
: 가속화된 이온을 웨이퍼 표면에 주입시키는데, Beam Scan 방식은 일반적으로 낮은 Dose의 이온을 주입할 때 사용하고, 이온 빔들을 x-y축으로 조절하여 최종적으로 웨이퍼 분사 위치 및 스캔 속도를 조절한다. 일반적으로 이온빔의 스캔 각도는 약 8(7)도 정도 기울어진 상태인데, 이는 대표적인데 이는 이온 주입의 문제점인 Channeling effect를 방지하기 위함이다.
*Channeling effect
: 단결정 구조처럼 원자 배열이 규칙이 있으면, 이온을 주입할 때 입사각에 따라 원자 배열 사이로 이온이 깊숙하게 도달하는 경우가 있는데 이를 Channeling Effect라고 한다. Channeling Effect는 결정의 구조, 이온 주입 입사각, 이온의 종류, 주입 에너지에 따라 영향을 받으며 Doping Profile에 부정적 영향을 준다.
⑤ 웨이퍼 이송장치(Handler) 및 페러데이 컵(Faraday Cup) - 웨이퍼 이송장치(Handler)는 반도체 제조 과정에서 웨이퍼를 다루고 페러데이 컵(Faraday Cup)은 입자 빔을 측정
: 웨이퍼 이송장치는 장비 특성에 따라 정확한 dose control이 필요한 medium/high 장비들과 생산성 향상을 위해 배치장피를 상용하는 고 에너지장비로 크게 분류된다. 빔 가이드를 통과한 빔이 최종적으로 웨이퍼에 입사되어 이온이 주입되며, 주입된 이온 농도는 웨이퍼와 동일 선상에 놓은 이온농도 측정기인 패러데이 컵에서 측정한다. 패러데이 컵은 떨어지는 이온들의 전류량을 실시간 측정하는 일종의 전류계이다.
⑥ 진공시스템 - 고진공을 유지하기 위한 시스템
: 이온 주입은 단일질량만을 가진 이온들만을 분리하고 유지하기 위해 고진공이 요구된다. 고진공하에서는 입자들의 평균이동거리(mean free path)가 확보가 용이하여 이온들의 상호 충돌로 인한 문제점을 예방할 수 있다. 주입의 진공시스템은 mechanical pump - Turbo Pump - Cryo Pump 순으로 되어 진공도를 높인다.
▶2. 급속 열처리(Rapid Thermal Processing: RTP)장비
(1) RTP 장비의 구조 및 특성
: RTP 장비의 구조는 크게 가열 시스템, 기체 제어 시스템, 온도 측정 시스템으로 구성된다. 가열 시스템은 반도체 웨이퍼를 가열하는데 사용되는 열원으로, 보통 램프나 히터로 이루어져 있다. 기체 제어 시스템은 반도체 웨이퍼의 가열 동안 기체 환경을 제어하는데 사용되며, 보통 진공 또는 산소, 질소 등의 기체를 사용한다. 온도 측정 시스템은 반도체 웨이퍼의 온도를 측정하는데 사용되며, 보통 광섬유 온도계 또는 적외선 온도계 등의 센서를 사용한다.
(2) RTP 램프 위치에 따른 공정 특성
: RTP 장비의 램프 위치는 반도체 소자의 가열 특성에 영향을 미친다. RTP 장비는 보통 상부 가열 방식과 하부 가열 방식으로 구분된다. RTP 시스템에서는 램프를 가열 챔버의 상단, 하단 또는 측면에 위치시킬 수 있다. 램프의 위치는 공정의 시간, 온도 분포 등의 특성에 영향을 미치기 때문에, 반도체 제조 공정에 따라 적절한 램프 위치를 선택해야 한다. 이 위치에 따라 다음과 같은 공정 특성이 나타난다. 각각의 방식에 따른 공정 특성은 다음과 같다.
(3) 상부 가열 방식과 하부 가열 방식의 특징
① 상부 가열 방식
상부 가열 방식은 램프가 반도체 웨이퍼의 상단에 위치하여 웨이퍼를 위쪽에서 가열하는 방식이다. 이 방식은 웨이퍼의 가열 온도를 빠르게 올리는 데 유용하며, 웨이퍼의 가열 평균 온도 분포를 넓게 만들 수 있다. 또한, 상부 가열 방식은 웨이퍼의 전체적인 가열 시간이 짧아 생산성을 높일 수 있다. 그러나 웨이퍼의 하부와 상부 온도 차이가 크게 나타나며, 웨이퍼의 열응력이 높아질 수 있다.
② 하부 가열 방식
하부 가열 방식은 램프가 반도체 웨이퍼의 하단에 위치하여 웨이퍼를 아래쪽에서 가열하는 방식이다. 이 방식은 웨이퍼의 하부 온도를 빠르게 올리는 데 유용하며, 웨이퍼의 가열 평균 온도 분포를 좁게 만들 수 있다. 또한, 하부 가열 방식은 웨이퍼의 열응력이 낮아지므로, 소자의 품질을 개선할 수 있다. 그러나 웨이퍼의 가열 시간이 더 길어지며, 생산성이 낮아질 수 있다.
따라서 RTP 장비의 램프 위치는 반도체 소자의 가열 특성과 생산성 등을 고려하여 선택되어야 한다. 램프 위치를 선택함으로써 웨이퍼의 가열 온도와 분포, 열응력, 생산성 등의 요소를 조절할 수 있다.
▶3. 가열로(Furance)장비
(1) 가열로 장비의 구조 및 특성
①카세트(또는 캐리어) 스테이지 - 웨이퍼가 보관
: 가열로에서 카세트 스테이지(Cassette stage)는 로딩장치와 가열 챔버를 연결하는 부분으로, 로딩장치에서 웨이퍼가 올라오면 카세트 스테이지에 장착된 카세트 안에 웨이퍼가 들어가게 된다. 그리고 가열 챔버 쪽에는 웨이퍼를 받아들이는 플레이트가 위치하고 있으며, 이 플레이트가 가열 챔버 안으로 웨이퍼를 이동시켜 가열을 수행한다. 카세트 스테이지는 웨이퍼의 이동을 제어하며, 웨이퍼를 카세트에서 받아서 가열 챔버로 이송시키는 역할을 한다. 이 때 카세트 스테이지는 보통 직선 운동을 수행하며, 웨이퍼 이송에 따라 위치를 정확하게 조절할 수 있다. 또한 여러 개의 카세트 스테이지를 사용하여 다양한 웨이퍼를 동시에 처리할 수도 있다. 카세트 스테이지는 로딩장치와 가열 챔버 간의 웨이퍼 이송을 원활하게 수행하기 위한 중요한 장치이며, 반도체 제조 공정에서 웨이퍼의 이동을 정확하게 제어함으로써 공정의 안정성과 품질을 보장한다.
② 포크(fork) - 웨이퍼 이송 제어를 담당
: 가열로는 대개 카세트(cassette) 스테이지(stage)와 동일한 수의 램프를 가지고 있다. 램프는 웨이퍼를 가열하는 역할을 하며, 각 램프는 일정한 온도 범위를 유지한다. 이때, 포크(fork)는 카세트 스테이지(stage)에 웨이퍼를 적재할 때 사용된다. 포크는 일종의 로봇 팔로, 웨이퍼를 자동으로 적재하고 반출하는 역할을 한다. 일반적으로, 포크는 웨이퍼를 다루는 로봇 팔의 일종으로, 수평 방향과 수직 방향으로 이동할 수 있다. 포크는 웨이퍼를 안전하게 적재하고 반출하기 위해, 특별한 집게(clamp)를 사용하기도 한다. 가열로에서는 일반적으로, 한 번에 여러 개의 웨이퍼를 처리하기 위해 포크를 사용한다. 이때, 포크는 각각의 램프에 웨이퍼를 적재하고, 처리가 완료된 웨이퍼를 반출하여 다음 단계로 전달한다. 포크는 여러 개의 램프를 처리하기 위해, 일반적으로 다중 포크(multi-fork)로 구성된다.
③ boat - 수백 매의 웨이퍼의 로딩이 가능한 슬롯을 가져 웨이퍼를 안전하게 이송
: 가열로 장비에서 boat(보트)는 대개 웨이퍼를 담는 컨테이너 역할을 한다. 보트는 일반적으로 금속으로 만들어진 직사각형 모양의 트레이(tray) 형태이며, 웨이퍼를 일정한 간격으로 배열할 수 있도록 디자인되어 있다. 보트는 대개 가열로에서 사용되는 웨퍼의 크기에 따라 다양한 크기와 형태로 제공된다. 보트는 일반적으로 웨이퍼를 안전하게 보관하고 이동시키는 역할을 한다. 보트는 일반적으로 수동으로 다루지만, 일부 고급 가열로 장비에서는 자동으로 보트를 이동시키는 로봇 시스템을 사용하기도 한다. 가열로 공정에서는 웨이퍼가 보트에 적재되어 처리되는데, 보트는 가열로 내부에서 특정한 경로를 따라 움직이면서 각 램프에서 처리되는 웨이퍼를 꺼내고, 다음 램프로 이동하면서 다시 적재한다. 이렇게 가열로 공정에서 웨이퍼를 안전하게 보관하고, 효율적인 처리를 위해 사용된다.
④ 가스 jungle box - 공정용 가스의 통합 조절장치
: 가열로 장비에서 가스 jungle box(가스 정글 박스)는 일종의 가스 공급 시스템이다. 가열로 공정에서는 보통 고순도 가스가 사용되는데, 이 가스를 공급하기 위해 가스 정글 박스가 사용된다. 가스 정글 박스는 일반적으로 가열로 공정에서 사용되는 다양한 가스들을 저장하는 데 사용된다. 가스 정글 박스 내부에는 가스의 순도를 유지하기 위한 다양한 필터 및 제어 장치가 장착되어 있다. 가스 정글 박스는 일반적으로 가열로 공정에서 사용되는 다양한 가스들을 저장하고 공급하기 위해 사용된다. 가스 정글 박스 내부에서 가스는 필터링되고 제어되어 가열로 공정에서 안전하게 사용될 수 있도록 보호된다. 이를 통해 가열로 공정에서 웨이퍼가 고품질로 처리될 수 있다.
⑤ burning box(또는 touch) - 가열로 내부에서 사용된 가스를 처리하는 장치
: 가열로 장비에서 가스 burning box(가스 버닝 박스)는 가열로 내부에서 사용된 가스를 처리하는 장치이다. 가열로 공정에서 사용된 가스는 보통 고순도 가스이며, 처리되지 않은 상태로 방출되면 환경오염과 안전 문제를 일으킬 수 있다. 따라서 가열로 공정에서 사용된 가스는 보통 가스 burning box를 통해 처리된다. 가스 burning box는 일반적으로 가열로 내부에서 사용된 가스가 집중적으로 배출되는 지점에 위치하며, 가열로 내부로 들어오는 새로운 가스와 혼합되어 연소한다. 이렇게 연소된 가스는 대기 중에 배출된다. 가스 burning box는 가열로 공정에서 사용된 가스를 안전하게 처리하고, 환경오염을 방지하기 위해 사용된다. 또한 가스 burning box는 가열로 공정에서 발생하는 열을 회수하여 다시 사용할 수 있도록 하는 열 회수 장치도 포함할 수 있다. 이렇게 열을 회수하면 가열로 공정의 에너지
효율을 높일 수 있다.
⑥ 히터 - 일반적으로 고온 및 고압가스를 가열할 때 사용
: 가스가 resistance coil을 지나가면 전기적 저항이 증가하며, 이로 인해 열이 생성된다. 이 열은 가스를 가열하고, 일정한 온도로 유지할 수 있다. 이 방법은 일반적으로 가스의 순도를 유지할 수 있기 때문에 반도체 및 전자 제조 공정에서 사용된다. 이 히터는 강성 및 내구성이 뛰어나며, 다양한 온도 범위에서 사용할 수 있다. 히터는 일반적으로 긴 히터 모듈에서 여러 개의 resistance coil로 구성되어 있으며, 이를 통해 가스를 균일하게 가열할 수 있다. 히터를 사용하는 가열로 공정은 일반적으로 높은 온도와 압력에서 가스를 처리하는 데 사용된다. 이 방법은 가스의 순도를 유지하면서 높은 처리량을 유지할 수 있으며, 일반적으로 반도체 및 전자 제조 공정에서 사용된다.
⑦ 펌프 - 반응 가스 공급 및 배출
: 일반적으로 진공 펌프 또는 양압 펌프가 사용된다. 진공 펌프는 가열로 내부의 공기를 제거하고, 가스를 흡입하여 압력을 낮추는 데 사용된다. 반면 양압 펌프는 가열로 내부에 가스를 공급하여 압력을 높이는 데 사용된다. 이 두 가지 펌프를 결합하여 가열로 내부의 압력과 순환을 조절할 수 있다.
⑧ 밸브 - 가열로 내부의 가스 흐름을 제어
: 일반적으로 온도 및 압력에 강한 재료로 만들어진 밸브가 사용된다. 밸브는 전기 신호나 수동 조작을 통해 열고 닫을 수 있으며, 가열로 내부의 가스 순환을 제어하고 가열로의 온도와 압력을 조절할 수 있다.
(2) 가열로 장비의 주요 Unit
① 웨이퍼 이송장치(Transfer unit 또는 Loading/Un-loading)
: 웨이퍼 이송장치는 가열로 내부에서 웨이퍼를 이동시키는 데 사용된다. 보통 로봇 암이나 컨베이어 벨트와 같은 장치가 사용된다. 웨이퍼는 이러한 장치를 통해 가열로의 각 공정 단계로 이동된다.
② 가열장치(Heating Unit)
: 가열장치는 웨이퍼에 열을 가하는 데 사용된다. 일반적으로 가열로 튜브에 내장된 resistance coil을 통해 웨이퍼에 열을 가한다. 가열장치는 웨이퍼를 특정 온도로 가열하여 반도체 및 전자 부품의 생산을 위한 적절한 온도 조건을 유지하기 위해 사용된다.
③ 가스 공급 장치
: 가스 공급 장치는 가열로 내부에 가스를 공급하는 데 사용된다. 이러한 가스는 반도체 및 전자 부품의 생산에 필요한 여러 공정을 수행하기 위해 사용된다. 일반적으로 산소, 질소, 아르곤, 헬륨 등의 가스가 사용된다.
④ 가열로 튜브
: 가열로 튜브는 가열로 내부에 있는 가열장치와 웨이퍼 이송장치를 감싸는 튜브이다. 이러한 가열로 튜브는 가열로 내부의 온도와 압력을 조절하기 위해 사용된다.
⑤ 제어 장치(Control Unit)
: 제어 장치는 가열로의 온도, 압력 및 가스 공급량 등을 제어하는 데 사용된다. 이러한 제어 장치는 반도체 및 전자 부품의 생산을 위한 정확한 온도 및 압력을 유지하기 위해 사용된다.
⑥ 펌프 장치
: 펌프 장치는 가열로 내부에 가스를 공급하고, 내부의 공기를 제거하는 데 사용된다. 일반적으로 진공 펌프와 양압 펌프가 사용된다.
⑦ Scrubber 장치
: Scrubber 장치는 가스를 정화하고, 환경오염을 방지하기 위해 사용된다. 이러한 Scrubber 장치는 가열로 내부에서 발생하는 가스를 처리하고, 환경에 미치는 영향을 최소화하기 위해 사용된다.
⑧ 전원공급장치(Electric Power Box)
: 가열로 운전에 필요한 전원을 공급하는 장치이다. 주로 고압과 고전력이 사용된다.
⑨ 배기장치(Exhaust Unit)
: 가열로 내부의 오염물질을 배출하는 장치로, 정화된 가스를 외부로 배출하거나 다시 가열로 내부로 회수한다.
⑩ 냉각수
: 가열로의 내부 온도를 조절하기 위한 냉각수이다. 가열로 내부의 열교환기 등을 통해 냉각수를 순환시켜 가열로 내부의 온도를 조절한다.
(3) 가열로 장비의 온도제어 방식
: 가열로 장비의 온도 제어 방식은 다양합니다. 가장 기본적인 방식은 온도 센서를 사용하여 가열로 내부의 온도를 감지하고, 이를 피드백 하여 히터의 전류를 조절하는 방식입니다. 이 방식은 비교적 간단하지만, 온도 제어 정확도가 낮을 수 있다. 더욱 정확한 온도 제어가 필요한 경우에는 PID 제어 방식을 사용하기도 합니다. PID 제어는 Proportional, Integral, Derivative의 약자로, 온도를 피드백 하여 P, I, D 값의 비율을 조절하여 정확한 온도를 유지한다. 또한, 가열로 내부의 온도가 불균일할 경우에는 Zoning 기법을 사용하기도 한다. 이 방식은 가열로를 여러 개의 영역으로 분할하여 각 영역의 온도를 독립적으로 제어하여 온도 균일성을 높인다.
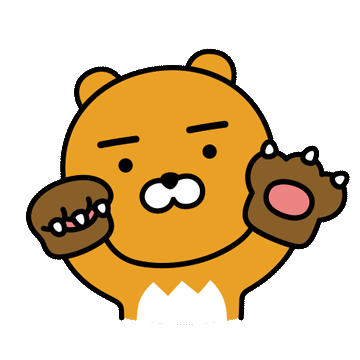
'Semiconductor > Semiconductor Fabrication' 카테고리의 다른 글
[반도체 공정] Moore's Law & Huang's Law (무어의 법칙 & 황의 법칙) (0) | 2024.05.15 |
---|---|
[반도체 공정] 플라즈마 공정, 플라즈마 장비 (0) | 2024.05.15 |
[반도체 공정] 패키징 공정, 패키징 장비 (0) | 2024.05.14 |
[반도체 공정] 박막 공정, 박막 공정 장비 (0) | 2024.05.13 |
[반도체 공정] 웨이퍼 제조, 웨이퍼 제조 장비 (0) | 2024.05.07 |
전자공학 블로그에 오신 것을 환영합니다! 최신 기술 동향, 회로 설계, 반도체 및 전자 부품에 대한 유용한 정보와 실습 팁을 제공합니다.