![[반도체 공정] 패키징 공정, 패키징 장비](https://img1.daumcdn.net/thumb/R750x0/?scode=mtistory2&fname=https%3A%2F%2Fblog.kakaocdn.net%2Fdn%2FEgMj7%2FbtsHnYeu3p6%2FaUuagxfNbcju39sSvUvWmK%2Fimg.png)
- ※1. 반도체 조립기술의 이해
- ▶1. 집적도의 한계와 구조 변화
- ▶2. 패키지(반도체 조립)
- ▶3. 반도체 조립기술의 역사 및 발전
- ▶4. 상부구조 형성기술
- ▶5. 리드 프레임과 기판
- ▶6. 반도체 패키지의 하부구조(Solder Ball) 형성기술
- ▶7. 칩 패키징 기술
- ▶8. 반도체 조립 공정기술의 분류 및 목적
- ※2. 반도체 조립기술의 이해
- ▶1. 후면 연삭(Back Grinding) & 다이 소잉(Die Sawing) 기술
- ▶2. 웨이퍼 후면 연삭 공정에서 사용되는 기술
- ※3. 다이 부착(Die Attach) & 와이어 본딩(Wire Bonding) 기술
- ▶1. 다이 부착(Die Bonding) 기술
- ▶2. 와이어 본딩(Wire Bonding) 기술
- ※4. 범프(Bump) 기술과 플립 칩 패키지(Flip chip package) 기술의 특징
- ▶1. 범프(Bump, Solder Ball) 기술
- ▶2. 플립 칩 패키지(Flip Chip Package) 기술의 특징
- ※5. 몰딩(Molding) 기술과 마킹(Marking) 기술
- ▶1. 몰딩(Molding) 기술
- ▶2. 마킹(Marking) 기술
- ※6. 반도체 조립 장비의 특성
- ▶1. 후면 연삭(Back Grinding) 장비 기술
- ▶2. DAF(Dicing Attach Film 또는 Tape Mounting) 장비 기술
- ▶3. 다이아몬드 블레이드(날)를 이용한 다이 소잉(Die Sawing 또는 Dicing) 장비 기술
- ▶4. DBG(Dicing Before Grinding, 연삭 전 절단) 및 레이저 소잉(Sawing) 장비기술
- ※7. 다이 부착(Die Attach, Bonding)&와이어 본딩(Wire Bonding) 장비기술
- ▶1. 다이 부착 장비 구성
- ▶2. 다이 부착 Flow
- ▶3. 다이 부착(Die Attach) 장비의 핵심기술(Die Ejector)
- ▶4. 와이어 본딩 장비기술
- ※8. 범핑 장비기술
- ▶ 범핑 장비
- ※9. 몰딩(Moiding) & 마킹(Marking) 장비기술
- ▶1. 몰딩 장비 Flow
- ▶2. 마킹 장비의 요소기술
안녕하세요.
이번시간에는 최근 미세공정의 한계에 국면하면서 가장 핫한 공정으로 손꼽히는 패키징 공정에 대해 알아보겠습니다.
아래는 다양한 다른 반도체 공정 과정과 장비를 설명 드리고 있습니다. 참고해보세요.
0.반도체 8대 공정
https://semicircuit.tistory.com/144
1.웨이퍼 제조, 웨이퍼 제조 장비
https://semicircuit.tistory.com/17
2. 박막 공정, 박막 공정 장비
https://semicircuit.tistory.com/48
3. 패키징 공정, 패키징 장비
https://semicircuit.tistory.com/52
4. 이온 주입 공정, 이온 주입 장비
https://semicircuit.tistory.com/53
5. 플라즈마 공정, 플라즈마 장비
https://semicircuit.tistory.com/54
6. 노광 공정, 노광 장비
https://semicircuit.tistory.com/57
7. 세정 공정, 세정 장비
https://semicircuit.tistory.com/59
8. 식각 공정, 식각 장비
https://semicircuit.tistory.com/60
※1. 반도체 조립기술의 이해
▶1. 집적도의 한계와 구조 변화
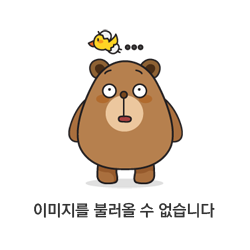
: 집적도는 반도체 칩 내에 트랜지스터를 얼마나 많이 집적시킬 있는지를 나타내는 지표이다. 집적도는 반도체 산업에서 지속적으로 증가하고 있지만, 어느 시점에서는 물리적인 한계에 도달한다. 집적도 한계에 도달하면 반도체 칩은 더 이상 작아질 수 없다. 따라서 패키징은 작은 공간 내에 칩을 효과적으로 배치하고 칩의 안정성을 보장해야 한다.
▶2. 패키지(반도체 조립)
: 반도체 패키징은 반도체 칩을 보호하고 외부와의 상호 작용을 용이하게 하기 위해 사용되는 프로세스이다. 패키징은 칩을 보호하는 역할을 수행하며, 칩의 물리적인 손상, 환경적인 영향, 열 및 전기적인 특성 등에 대한 안정성을 제공한다. 또한 패키징은 칩을 다른 시스템과 연결하고, 신호와 전력을 전달하는 인터페이스 역할을 수행한다.
<반도체 패키지의 구성 요소별 기능>
① 기판[Substrate] : 패키지의 기반이 되는 재료로서, 반도체 칩을 마운트하고 패키지의 구성 요소들을 연결하는 역할을 한다. 주로 실리콘, 세라믹, 플라스틱 등의 재료로 제작되며, 패키지의 물리적 지원과 전기적 연결을 위한 플랫폼 역할을 수행한다. 기판은 다중 레이어를 가질 수 있으며, 내부 레이어는 신호 및 전력 전달을 위한 경로를 형성한다.
② 금속선[Metal Wire] : 금속선은 칩과 패키지 간의 전기적인 연결을 위해 사용되는 선이다. 이러한 금속선은 보통 알루미늄, 금, 구리 등의 금속으로 제작되며, 칩의 핀과 패키지의 핀 또는 기판 간의 연결을 제공한다. 금속선은 전기 신호와 전력을 전달하고 칩 내의 다른 구성 요소들과 상호 작용하게 해준다.
③ 솔더 볼/리드 프레임 : 솔더 볼/리드 프레임은 패키지의 외부 연결을 담당한다. 이는 주로 소형 볼 형태로 제작되며, 패키지의 바닥에 위치한다. 솔더 볼/리드 프레임은 패키지와 다른 시스템 간의 연결을 위한 인터페이스 역할을 하며, 필요에 따라 솔더링 프로세스를 통해 외부 회로나 인터페이스와 연결된다.
④ 몰딩 화합물 : 몰딩 화합물은 패키지의 보호와 봉인을 위해 사용되는 재료이다. 주로 플라스틱 또는 에폭시로 제작되며, 칩과 다른 패키지 구성 요소들을 보호하고 외부 요소로부터 칩을 차폐하여 안전한 운영을 가능하게 한다. 몰딩 화합물은 물리적 충격, 습기, 열, 먼지 등의 외부 환경 요소로부터 칩을 보호하고 전기적 특성을 안정화시키는 역할을 한다. 또한 패키지의 외관을 형성하고 마감을 제공하여 식별 가능하도록 한다.
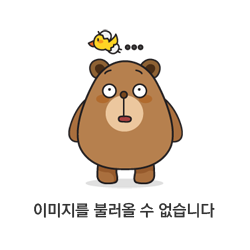
▶3. 반도체 조립기술의 역사 및 발전
: 반도체 조립기술은 크게 리드프레임 -> BGA(Ball Grid Array) -> 3차원 적층기술로 나뉜다.
① Lead Frame(Through hole wave)
: 리드프레임 조립 기술은 초기 반도체 패키징 기술 중 하나이다. 이 기술에서는 솔더 볼과 연결된 리드프레임이 패키지의 하단에 위치한다. 반도체 칩은 리드프레임 위에 마운트되고, 칩과 리드프레임 간에 와이어 본딩을 통해 전기적인 연결이 이루어진다. 리드프레임은 패키지의 외부 연결을 담당하며, 일반적으로 DIP (Dual In-line Package) 형태로 사용된다.
② PCB(SMT->Area Array->HDI wave)
: BGA는 리드프레임에 대한 대안으로 개발된 패키징 기술이다. BGA에서는 칩의 하단에 솔더 볼이 배열된 그리드가 있으며, 패키지의 기판 상에 대응하는 솔더 패드가 있다. 칩은 솔더 볼과 패키지의 솔더 패드를 연결하기 위해 재료를 녹여 솔더링하는 과정을 거친다. BGA는 리드프레임에 비해 더 밀도 높은 핀 수와 좋은 전기적 성능을 제공하며, 더 낮은 전기 저항과 더 높은 신호 전송 속도를 가능하게 한다.
③ Semiconductor Process(3D integration)
: 3차원 적층 기술은 최근에 개발된 반도체 조립 기술 중 하나이다. 이 기술은 여러 개의 반도체 칩을 수직으로 적층시키는 것을 의미한다. 각 칩은 연결 통로를 통해 데이터와 전력을 교환할 수 있다. 3차원 적층 기술을 사용하면 공간 효율성을 향상시킬 수 있으며, 다중 칩 시스템을 하나의 패키지에 통합함으로써 성능을 향상시킬 수 있다. 이러한 기술은 더 작은 공간에 더 많은 기능을 포함하는 고밀도 반도체 시스템에 유용다.
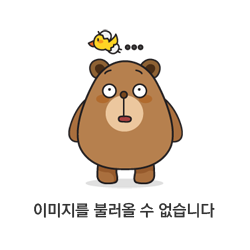
▶4. 상부구조 형성기술
: 반도체 칩과 기판을 연결하는 방식은 미세 금(Au) 배선을 이용하여 전기적으로 연결하는 와이어 본딩 방식과 칩에 돌기 형태의 범프(Bump)를 형성하여 기판과 직접 연결하는 범핑 방식이 있다.
① 와이어 본딩 방식(Wire Bonding) 6가지 제조기술
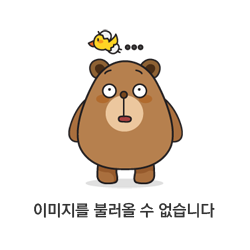
- 정제 : 순도 99.99%의 금괴를 사용하지만 추가로 순도를 변경
- 용해 : 금을 wire 형태로 가공하기 위해 용해
- 주조 : 용해된 금을 손가락 굵기의 wire 형태로 변형
- 신선(Drawing) : 굵은 wire를 좁은 구멍으로 통과시켜 원하는 두께 형성
- 열처리 공정 : 경화현상 방지, 신선 과정 중 수행
- 권선(wiring) : 최종 출하를 위해 wire를 감는 과정
② 범핑 방식(Bumping Bonding) 4가지 제조기술

- 금속 마스크(mask)나 웨이퍼 위에 다른 방식의 솔더 마스크(solder mask)를 사용하여 솔더를 증착(evaporation)시키는 방법
- 솔더를 전해도금(electroplating) 방식을 제조하는 방법
- 솔더 페이스트(solder paste)를 사용하여 패드 상에 인쇄한 후, 리플로우 (reflow)하여 솔더를 형성한느 방법(screen printing)
- 기타 솔더 볼 탑재, Super-Juffit 및 스터드(Stud) 방법
▶5. 리드 프레임과 기판
① 리드 프레임 : 리드 프레임은 패키지의 외부 연결을 위한 구성 요소로 사용되는 소형 금속 프레임이다. 주로 알루미늄, 구리 또는 합금으로 만들어지며, 다수의 솔더 볼과 연결된 형태로 제작된다. 리드 프레임은 패키지와 외부 시스템 간의 연결 인터페이스 역할을 수행한다.
② 패키지 기판 제조 : 패키지 기판은 반도체 칩을 마운트하고 패키지의 구성 요소들을 연결하기 위한 플랫폼 역할을 수행한다. 기판 제조 과정은 다음과 같은 단계로 구성된다.
▶6. 반도체 패키지의 하부구조(Solder Ball) 형성기술
: 리드 프레임은 그 자체로 주료 PCB(Board)와 연결하는 기판 역할을 하기 때문에 패키지 하부구조는 기판(BGA)와 주요 PCB를 연결하기 위한 솔더 볼(Solder ball) 기술로 제한된다.
솔더 볼(Solder ball) 기술은 PCB(Printed Circuit Board)를 다른 장치나 컴포넌트와 연결하기 위해 사용되는 기술이다. 솔더 볼은 솔더로 만들어진 작은 구 형태의 볼로, PCB의 솔더 패드와 다른 장치 또는 컴포넌트의 연결점 사이에 위치한다. 이 볼은 솔더 패드와 솔더 볼 자체의 용융 상태를 이용하여 연결이 형성되는데, 이를 솔더링(Soldering)이라고 한다.
▶7. 칩 패키징 기술
① SIP(System in Package) 기술
: SIP는 System in Package의 약자로, 여러 개의 다양한 칩이나 컴포넌트를 한 패키지에 통합하는 기술이다. SIP는 칩이나 컴포넌트 간의 통신을 용이하게 하고, 공간을 절약하며, 전력 소비를 줄이는 장점을 가지고 있다. SIP 패키지는 다양한 기술을 사용하여 구현될 수 있으며, 패키지에는 다수의 다이(Die)가 적층되거나, 다이와 다이 사이에 인터프로젝트 연결 기술이 사용될 수 있다.

② WLCSP(Wafer-Level Chip Scale Packaging)
: WLCSP는 칩 스케일 패키징의 한 형태로, 웨이퍼 수준에서 칩을 패키징하는 기술이다. WLCSP는 솔더볼 없이 다이의 패딩을 직접 연결하여 작은 크기와 낮은 프로파일을 가진 패키지를 제공한다. 이 기술은 표면 마운트 기술로 직접 다이를 웨이퍼에서 적층시키고, 각 다이 간의 전기적 연결을 위해 선호 패딩 기술을 사용한다. WLCSP는 고밀도와 고성능 요구 사항을 충족시키는데 적합하며, 주로 소형 모바일 디바이스 및 웨어러블 기기에 사용된다.
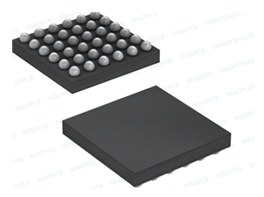
③ FoWLP(Fan-out Wafer-Level Packaging)
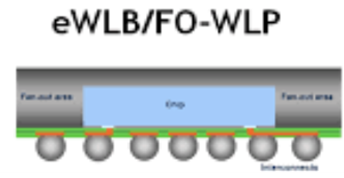
: FoWLP는 웨이퍼 수준에서 다이와 다이 사이에 고밀도 패키징을 제공하는 기술이다. FoWLP는 웨이퍼 위에 다이를 배치한 뒤, 패키지 전체를 봉합하여 완성시킨다. 이 과정에서 다이 주위에 패키지 및 전선 연결을 위한 패딩 및 기타 구성 요소를 추가할 수 있다. FoWLP는 고밀도의 다이 및 다이 간 연결을 지원하며, 다이 사이의 전기 및 신호 전달을 향상시킨다. 이 기술은 작은 크기와 낮은 프로파일을 가지며, 주로 고성능 처리 및 통신 애플리케이션에 사용된다.
④ 3D TSV(Through Silicon Via) Package 기술
: 3D TSV(Through Silicon Via) Package 기술은 칩을 적층시켜 3차원 구조로 패키징하는 기술이다. TSV는 칩의 실리콘 다이를 통해 수직으로 구성된 작은 구멍이며, 이를 통해 다이 간의 전기적 및 신호 연결이 가능해진다. TSV 패키지는 높은 성능, 낮은 전력 소비, 작은 크기 등의 이점을 제공한다.
⑤ 인터포저(Interposer) 응용 TSV 패키지 기술
: 인터포저(Interposer) 응용 TSV 패키지 기술은 TSV 패키지를 구성하는 한 가지 방법으로, 다이와 다이 사이에 인터포젝트(Interposer)를 사용하여 전기적 연결과 신호 전달을 제공하는 기술이다. 인터포젝트는 일종의 중개 장치로서, 다이와 다이 간의 통신을 용이하게 하며 다양한 기능을 추가할 수 있는 장점을 가지고 있다.
⑥ 유연 칩 패키지(Flexible Chip Package) 기술
: 유연 칩 패키지(Flexible Chip Package) 기술은 칩을 유연한 기판 또는 서브스트레이트에 패키징하는 기술이다. 이러한 기술은 유연한 소재를 사용하여 칩을 보호하고 전기적 연결을 제공하는 동시에 패키지의 유연성과 기계적 강도를 향상시킨다.
▶8. 반도체 조립 공정기술의 분류 및 목적
- 후면 연삭(Back Grinding) 기술 : 웨이퍼의 후면을 100um 이하 두께로 가공
- 쏘잉(Sawing 혹은 Dicing) 기술 : 웨이퍼 칩을 개별 단위(die)로 분리 가공
- 다이 부착(Die Attaching) 기술 : 기판에 칩을 붙여 고정
- 와이어 본딩(Wire Bonding) 기술 : 금 또는 구리로 칩을 기판에 연결
- 몰딩(Molding) 기술 : EMC 재료로 칩이 실장된 기판을 보호
- 마킹(Marking) 기술 : 레이저로 패키지 표면에 제품정보를 입력
- 솔더볼 마운트(Solder Ball Mount) 기술 : 기판에 솔더 볼을 붙여 이웃단자 형성
- 패키징 소잉(Package Sawing) 기술 : 전자기기 실장을 위해 개별 반도체로 분리
※2. 반도체 조립기술의 이해
▶1. 후면 연삭(Back Grinding) & 다이 소잉(Die Sawing) 기술
: 후면 연삭기술은 조립기술에서 목표 웨이퍼 두께를 확보하기 위해 웨이퍼 후면 Si를 글라인딩 휠(grinding wheel)을 이용하여 원하는 두께까지 가공하는 기술이며, 웨이퍼 두께에 따라 여러 기술을 조합한다.
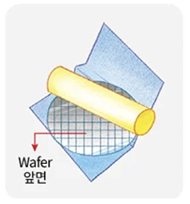
[100um 두께까지 가공] - 기계적 연삭 기술
[50um 두께까지 가공] - 기계적 연삭 + 연마(Polishing) 기술
[50um 이하 두께 가공] - DBG(Dicing Before Grinding) 기술
=> 후면 연삭기술은 모서리 절단(edge trimming), 테이프 마운팅(tape mouting), 기계적 연삭(mechanical grinding), 연마(polishing) 또는 식각(etching) 순서로 진행된다.
▶2. 웨이퍼 후면 연삭 공정에서 사용되는 기술
① 테이프 마운팅(Tape Mounting, Wafer Lamination, 테이브 부착) 기술
: 테이프 마운팅 기술은 칩 또는 다이 웨이퍼를 보호하고 다음 단계인 백그라인딩 또는 다이 소유로의 분리를 위해 테이프로 묶는 과정을 말한다. 이 과정은 다이의 안정성을 유지하고 외부 요소로부터 보호하기 위해 필요하다. 테이프는 일반적으로 폴리머 소재로 제작되며, 다이를 테이프에 부착한 후 후속 공정을 진행한다.
② TGM(Thin Griding Mounting) 기술
: TGM 기술은 다이를 얇게 연마하여 더 얇은 형태로 만드는 기술이다. 다이의 두께를 조절하고 제어하기 위해 다이를 적용한 후 연마 공정을 수행한다. 이를 통해 다이의 두께를 정확하게 조절할 수 있으며, 반도체 소자의 높은 밀도와 작은 크기를 달성할 수 있다.
③ DBG(Dicing Before Griding) 기술
: DBG 기술은 다이 소유로를 수행하기 전에 다이를 분리하는 과정을 의미한다. 이 과정에서는 다이 소유로 전에 다이를 정확하게 분리하기 위해 다이에 절단선을 생성한다. 일반적으로 다이 소유로는 완전한 다이를 보유하고 있는 웨이퍼를 말한다. DBG 기술은 소형화된 다이를 얻기 위해 필요한 과정이다.
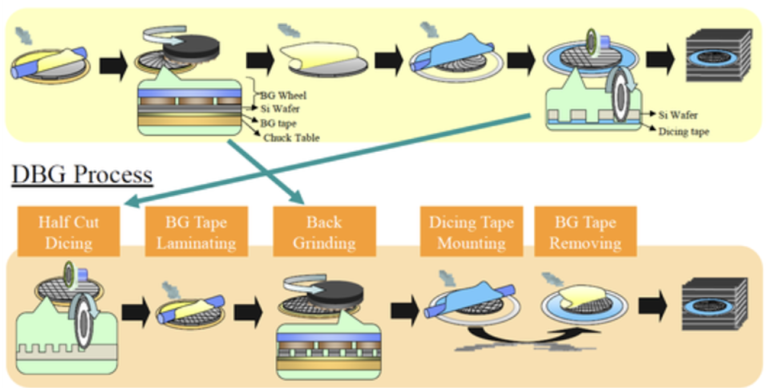
④ DAF(Dicing Attach Flim 또는 Wafer Mounting) 기술
: DAF 기술은 다이 소유로 공정에서 사용되는 기술로, 다이 소유로에 다이를 부착하는 과정을 의미한다. 이를 위해 다이 소유로에 접착 필름을 부착하고, 다이를 절단한 후 필름에 의해 다이를 보호한다. 이러한 과정은 다이의 안정성을 유지하고 외부 환경으로부터 보호하기 위해 필요하다.
⑤ 칩 분리(Die Sawing) 기술
: 칩 분리(Die Sawing) 기술은 다이를 개별적인 칩으로 분리하는 과정이다. 이 과정은 절단기로 다이 소유로에 존재하는 절단선을 따라 다이를 절단하여 개별 칩으로 분리한다. 이때 사용되는 절단기는 고정밀한 컷팅 블레이드를 갖추고 있으며, 다이 소유로에 부착된 다이를 정확하게 분리할 수 있다.
※3. 다이 부착(Die Attach) & 와이어 본딩(Wire Bonding) 기술
▶1. 다이 부착(Die Bonding) 기술
: 다이 부착 기술은 리드 프레임 또는 기판에 칩을 접착제로 고정한 다음, 오븐에서 약 175도에서 1시간동안 경화, 접착하는 것으로써 전지적 특성 및 신뢰성을 결정하는 기술이다. 접착제 소재는 에폭시 및 페놀(Phenol) 수지, 아세톤(acentone), 비 결정 실리카, 은, 유기 과산화물, 경화제 등을 사용한다.
칩을 테이프에 접착시키는 방법에는 고온과 하중을 이용하는 접착방식과, 엘라스트모(elastomer, 탄성중합체)를 인쇄방식으로 코팅하여 칩을 기판에 부착하는 및 주 PCB 위에 은 에폭시(silver epoxy) 또는 절연 에폭시를 타점(dotting)한 다음, 칩을 접착하여 경화시키는 방식이 있다.
▶2. 와이어 본딩(Wire Bonding) 기술
: 앞서 기술한 것처럼 와이어 본딩 기술은 금 또는 구리 와이어에 초음파, 열 및 힘을 가해 칩을 리드 프레임 또는 기판의 패드에 연결하여 PCB로부터 칩에 전원 공급이 가능하도록 하는 기술로 모든 패드를 연결해야하기 때문에 다른 기술에 비해 장시간의 작업이 요구된다.
<와이어 본딩의 종류>
① 열•초음파 방식 : 열-초음파 방식은 반도체 칩과 패키지 간에 와이어 본딩을 형성하는 데 사용되는 일반적인 방법 중 하나이다. 이 방식은 초음파와 열을 동시에 사용하여 와이어를 패드에 결합시킨다. 초음파는 와이어와 패드 사이의 물리적 접촉을 강화시키고, 열은 와이어와 패드 사이의 금속 결합을 형성하는 데 사용된다. 일반적으로 초음파 주파수는 수십 kHz에서 수백 kHz의 범위에 있으며, 열은 주로 압전 히터나 레이저를 통해 제공된다. 이 방식은 알루미늄 또는 금 와이어와 같은 소프트 본딩 와이어에 대해 효과적으로 사용된다.
② 쐐기(Wedge) 방식 : 쐐기 방식은 와이어를 웨이퍼나 패키지의 패드에 삽입하여 고정하는 와이어 본딩 방법이다. 이 방식에서는 와이어를 특수한 형태의 쐐기 또는 웨지에 의해 압착된다. 쐐기는 주로 알루미늄 또는 금속으로 만들어지며, 와이어를 패드에 고정하기 위해 압력을 가한다. 쐐기 방식은 웨이퍼 본딩 프로세스에서 사용되는 주요 기술이다.
③ 열•합착(Thermo Compression) 방식 :열-합착 방식은 와이어를 패드에 결합시키기 위해 열과 압력을 사용하는 와이어 본딩 기술이다. 이 방식에서는 와이어와 패드 사이에 열 및 압력을 가하고, 이로 인해 와이어와 패드 사이의 금속 결합이 형성된다. 일반적으로 열-합착은 알루미늄 와이어와 같은 높은 온도에서 소프트 본딩 와이어에 사용된다. 열-합착 방식은 보다 정밀한 제어가 필요한 응용 분야에서 사용되며, 보다 안정적인 연결을 제공한다.
※4. 범프(Bump) 기술과 플립 칩 패키지(Flip chip package) 기술의 특징
▶1. 범프(Bump, Solder Ball) 기술
: 주 PCB 칩을 직접 연결하는 범핑 기술과 칩을 반대 방향으로 위치하여 기판에 접합하는 페이스 다운(face down) 방식으로 범프를 이용하여 칩과 기판을 전기적 및 기계적으로 연결하는 플립 칩(Flip chip) 패키지 응용기술이 있다.
<기능>
① 기판 사이의 전기적, 기계적 연결 및 칩에서 발생한 열의 발산, 칩과 기판 사이 전기적 접촉 방지
② 작은 크기의 패키지 구현, I/O 수 증가
③ I/O 단자 재 분포를 통한 실장 밀도 확충
<기술 Flow>
① 초순수 세척(DI Scrubbing) - 칩 표면 불순물 제거
② 열처리 - 접착력 향상을 위한 수분제거
③ 물리적 증착(Sputtering) - 칩(또는 wafer) 표면에 솔더 범프(solder bump)의 접착력 및 전기적 특성을 향상시키기 위해 UBM을 증착
④ 감광막 코팅(PR coating) - 범프를 선택적으로 형성하기 위함
⑤ 노광(lithography) - 범프를 선택적으로 형성하기 위함
⑥ 현상(develop) - 범프를 선택적으로 형성하기 위함
⑦ 유기물 제거(de-scum) - 범프를 선택적으로 형성하기 위함
⑧ 범프 패턴용 전도성 금속막 증착 - PR(감광막 패턴 하부에 노출된 UBM을 씨드층으로 이용하여 전해 도금법으로 PB/Sn과 같은 합금 박막 형성
⑨ PR 제거(또는 Ashing) - 감광막 PR을 제거하여 범프 패턴만 형성
⑩ UMB 식각 기술 - 범프 패턴 주변에 노출된 UBM 박막 (Cu/Ti)을 에칭 백(etch back) 방식으로 제거, UBM 및 범프 적층 박막 패턴만을 잔류
⑪ IR 리플로어(Reflow) - 솔더 볼(Solder ball) 구조 형태로 변화, 범프 패턴과의 접착 향상
⑫ AVI(Auto Visual Inspection) - 칩 또는 웨이퍼 표면 불량 검사
⑬ 범프 높이 측정 - 접촉 또는 비접촉식으로 높이 차이를 측정
⑭ 전단(Shear) 본딩 검사기(Tester) - 범프 접착상태를 측정
▶2. 플립 칩 패키지(Flip Chip Package) 기술의 특징
① 패키지 특성이 우수하며, 칩과 기판 접속 길이가 짧아 임피던스가 매우 작다.
② 고속의 동작 주파수 조건에서는 입출력의 반사손실이 커서 패키지로써 부적합하다.
③ 50%이상의 I/O 수 증가를 기대할 수 있다.
④ 칩을 반대로 뒤집어서 접착하므로 기술 신뢰성 확보가 중요하다.
⑤ 후면 연삭 기술을 진행함에 따라 물리적 충격에 대응해야만 한다.
⑥ 칩의 크기가 크거나 스탠드 오프(stand-off)가 낮으며 공정시간이 증가하여 생산성을 감소시키고, 공동(void) 불량이 발생한다.
⑦ 습도에 민감하며, 고온에서 솔더 범프가 용해되어 빈 공간으로 분산되면서 번형 및 미성형(short) 불량이 발생한다.
※5. 몰딩(Molding) 기술과 마킹(Marking) 기술
▶1. 몰딩(Molding) 기술
: 몰딩(Molding) 기술: 반도체 패키징에서 몰딩은 반도체 칩을 보호하고 전기적 및 기계적 보안을 제공하기 위해 사용된다. 재료의 형상화와 경화를 위해 열과 압력을 사용하는 공정이다. 각각의 기술은 제품의 크기, 형태, 재료 특성, 생산량 등에 따라 선택되며, 다양한 산업 분야에서 활용된다. 몰딩(Molding) 기술 중에서 트랜스퍼 몰딩(Transfer Molding)과 컴프레션 몰딩(Compression Molding)으로 나눠진다.
-트랜스퍼 몰딩(Transfer Molding): 트랜스퍼 몰딩은 미리 정해진 형상의 금형에 플라스틱 또는 고무 등의 재료를 넣고 열과 압력을 가하여 형성하는 공정이다. 이 때, 재료는 속이 비어있는 피스톤(Plunger)을 통해 금형으로 전달된다. 금형 안으로 들어간 재료는 열과 압력에 의해 경화하고 형상에 맞게 형성된다. 트랜스퍼 몰딩은 고압을 이용하여 정확하고 반복 가능한 제품을 생산할 수 있으며, 고속 생산이 가능하다. 트랜스퍼 몰딩은 전자 부품, 오링, 고무 부품 등 다양한 제품에 사용된다.
-컴프레션 몰딩(Compression Molding): 컴프레션 몰딩은 재료를 금형에 넣고 압축하는 공정으로, 압력과 열을 가하여 재료를 형성한다. 재료는 미리 형성된 프레폼(Preform) 또는 원재료로 사용될 수 있다. 프레폼은 이미 형상화된 재료로서, 금형 안에 놓여 압력과 열에 의해 압축되고 경화된다. 컴프레션 몰딩은 비교적 간단한 장비와 저렴한 형상 성형 툴을 사용할 수 있어 경제적인 생산이 가능하다. 주로 고무 제품, 실리콘 제품, 열가소성 플라스틱 등을 생산하는 데 사용된다.

▶2. 마킹(Marking) 기술

: 마킹은 반도체 패키지에 식별 정보를 부여하는 과정으로 중요한 역할을 한다. 마킹은 제조사, 제품 코드, 일련번호, 날짜 등을 패키지 표면에 표시하여 추적성과 식별성을 제공한다. 반도체 패키징에서는 다양한 마킹 기술을 사용할 수 있다. 일반적으로 레이저 마킹, 잉크젯 마킹, 패드 프린팅 등이 사용된다. 레이저 마킹은 레이저를 사용하여 고해상도로 마킹을 생성하며, 잉크젯 마킹은 잉크를 사용하여 표면에 마킹을 인쇄한다. 패드 프린팅은 패드를 사용하여 잉크를 마킹 표면에 전달하는 기술로, 비교적 저렴하고 빠른 공정이다.
※6. 반도체 조립 장비의 특성
▶1. 후면 연삭(Back Grinding) 장비 기술
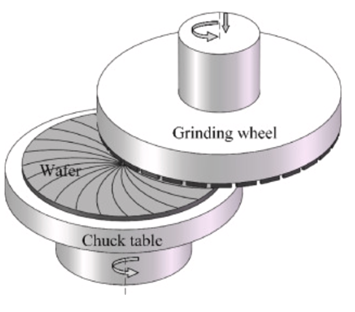
: 후면 연삭은 모서리 절단, 테이프 마운팅(tape mounting, laminating), 후면 연삭, 연마 및 테이프 제거 장비로 구성되어 있다.
① 모서리 절단 (Edge Trimming): 후면 연삭 공정 이전에는 웨이퍼의 모서리 부분에 보호막 또는 기타 재료가 적용되어 있을 수 있다. 이러한 재료를 제거하기 위해 모서리 절단이 수행된다. 일반적으로 다이아몬드 나사 블레이드를 사용하여 모서리를 절단한다.
② 테이프 마운팅 (Tape Mounting, Laminating): 웨이퍼의 후면에는 연마 과정에서 웨이퍼를 보호하기 위해 특수한 테이프가 부착된다. 테이프 마운팅은 웨이퍼의 후면에 테이프를 정확하게 부착하는 과정이다. 이를 위해 정교한 테이프 마운팅 장비가 사용된다. 테이프는 웨이퍼의 후면을 보호하고 고정하여 연마나 연삭 과정에서 웨이퍼가 손상되지 않도록 한다.
③ 후면 연삭 (Back Grinding): 후면을 고속 회전하는 연마 휠 또는 연마 패드와 함께 연마하는 과정이다. 이를 통해 웨이퍼의 두께를 일정하게 조절하고 후면을 평평하게 만든다. 연마는 정교한 제어가 필요하며, 고정밀한 장비와 적절한 연마 매체를 사용하여 수행된다.
④ 연마 및 테이프 제거 (Grinding and Tape Removal): 후면 연삭 후에는 연마 마침 과정이 진행된다. 이는 웨이퍼의 후면 표면을 보다 부드럽게 마무리하고 깨끗하게 만드는 작업이다. 또한, 테이프 제거도 이 단계에서 수행된다. 테이프는 웨이퍼의 후면에 남아있어 후면 연삭 후에는 테이프를 제거해야 한다. 일반적으로는 테이프 제거 장비를 사용하여 테이프를 천천히 제거하고, 웨이퍼의 후면을 깨끗하게 정리한다. 테이프 제거 장비에는 다양한 방식과 메커니즘이 사용될 수 있으며, 이는 테이프 종류와 웨이퍼의 특성에 따라 다르다.
⑤ 테이프 제거 과정: 테이프를 웨이퍼의 후면에서 부드럽게 분리하고 제거하는 것이 중요하다. 이는 웨이퍼 표면을 손상시키지 않으면서 테이프를 완전히 제거하는 것을 목표로 한다. 일부 장비는 열 또는 용매를 사용하여 테이프 접착력을 약화시키고 제거할 수 있다. 또한, 적절한 감압 및 제어된 속도로 작동하여 웨이퍼를 안전하게 처리한다.
▶2. DAF(Dicing Attach Film 또는 Tape Mounting) 장비 기술
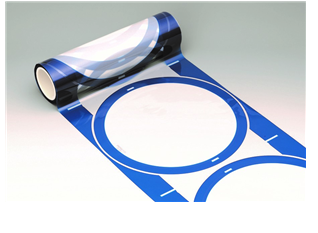
: Dicing Attach Film (DAF)은 반도체 패키징 공정에서 웨이퍼의 다이(Die)를 분리하기 위해 사용되는 특수한 접착 필름이다. DAF는 다이가 웨이퍼에 고정되고 이후에 다이를 분리하는 과정에서 장력을 완화하고 다이의 안정성을 보장하는 역할을 수행한다. DAF 장비는 카세트 로드 포트 모듈(load port module), 웨이퍼, DAF 및 다이싱 테이프 이송부(Dicing tape transfer), DAF 경화(curing) 및 접착 테이블 부, DAF 및 다이싱 테이프 절단부(dicing tape cutting), UV 광 스캐닝(light scanning) 부로 분류 된다.
<Wafer Flow>
① 웨이퍼 반송 테이블로 웨이퍼를 DAF 접착 테이블 상부까지 이동시킨다.
② 웨이퍼 이송 Arm이 DAF 전찹 테이블로 반송한다.
③ DAF 배치 절단부(batch cutting)의 내부에서 DAF를 웨이퍼 형태로 절단하는 배치 절단부를 탑재하여 DAF를 접착 테이블 부로 이동시킨다.
④ 웨이퍼 정렬부는 CCD 카메라로 웨이퍼 위치 결정 이후 Arm에 의한 절단 테이프(dicing tape) 접착 테이블로 이동시킨다.
⑤ 웨이퍼 이송 Arm로 DAF가 접착된 웨이퍼를 DAF 경화(curing) 및 다이싱 테이프 접착 테이블 부로 이동시킨다.
⑥ 링프레임(Ring frame) 공급부에서 프레임 이송 Arm은 링 프레임을 1장씩 흡착 유지하여 접착 테이블로 이동 시킨다.
⑦ 절단 테이프 공급기(dicing tape feeder)에서는 사전에 링 프레임 크기로 절단된 다이싱 테이프를 프레임에 부착한다.
⑧ 다이싱 테이프 접착 테이블에서 링 프레임과 웨이퍼 후면에 다이싱 테이프를 접학하며, 열 접착이 가능한 테이프를 사용하여 보호 테이프를 충전(fillinf)한다.
⑨ 전면 흡착 타입인 테이블이 소재를 흡착 고정하여 테이프 충전부, UV 광 스캐닝부로 이동한다.
▶3. 다이아몬드 블레이드(날)를 이용한 다이 소잉(Die Sawing 또는 Dicing) 장비 기술
: 다이 소잉(혹은 절단) 장비는 카세트 로딩 유닛, 웨이퍼 이송을 담당하는 상부 및 하부 Arm, 웨이퍼를 정렬하는 사전 정렬 스테이지(pre-alignment stage), 웨이퍼의 칩을 소잉하는 척 테이블, 웨이퍼를 세정 및 건조하는 회전부 테이블로 구성된다.
<Wafer Flow>
① 하부 Arm으로 카세트에서 웨이퍼를 픽업(pick-up) 하여 사전 정렬 스테이지로 이동시켜 절단을 위한 위치를 정밀하게 제어한다.
② 척 테이블로 이동시켜 웨이퍼의 칩 절단(분리)를 수행한다.
③ 상부 Arm으로 절단이 완료된 웨이퍼를 회전부 테이블로 이송한다.
④ 세정 및 건조 후 웨이퍼를 회전부 테이블로부터 카세트로 이동시켜 작업을 완료한다.
▶4. DBG(Dicing Before Grinding, 연삭 전 절단) 및 레이저 소잉(Sawing) 장비기술
: DBG 기술은 절반 절단(half cut dicing)을 위한 다이아몬드 블리에드를 이용한 다이싱 장비, 테이프 라미네이팅 장비, 후면 연삭(인라인 구성으로 연삭(grinding), 건조 연마(dry polishig), 테이프 제거(tape removing), DAF 테이프 마운팅(tape mountinf)작접) 장비 및 레이저 최종 절단(full cutting) 장비 등을 이용하여 진행한다.
레이저 소잉 장비는 카세트 로드부, 웨이퍼 이송용 상부 및 하부 Arm, 웨이퍼 사전 정렬 스테이지, 칩 소잉용 척 테이블, 웨이퍼 세정 및 건조의 회전부 테이블로 구성된다.
<Laser Sawing Wafer Flow>
① 프레임 선택부(Frame Pick Arm)는 카세트에서 웨이퍼를 사전 정렬 스테이지(Pre-alignment stage)로 이동시켜 웨이퍼의 중심잡기(centering)을 실시한다.
② 상부 Arm은 웨이퍼를 척 테이블로 이동, 칩을 레이저 소잉 한다.
③ 하부 Arm은 웨이퍼를 회전부 테이블로 이송, 세정 및 건조를 실시한다.
④ 상부 Arm은 웨이퍼를 사전 정렬 스테이지로 이동시킨다.
⑤ 프레임 선택 암(Frame Pick Arm)은 웨이퍼를 카세트로 이동시켜 작업을 완료한다.
※7. 다이 부착(Die Attach, Bonding)&와이어 본딩(Wire Bonding) 장비기술
▶1. 다이 부착 장비 구성
: 다이 부착 장비는 웨이퍼 로더, L/F 적재기 및 이송장치, 에폭시 헤드, 웨이퍼 카세트 스테이지, 웨이퍼 이송 장치, 웨이퍼 스테이지, 결합 헤드, 인텍서 및 언로더로 구성한다.
▶2. 다이 부착 Flow
① 기판(substrate 또는 pad)로딩 : 다이 부착 공정에서 사용할 기판(서브스트레이트)을 로딩한다. 기판은 다이가 부착될 표면을 가지고 있으며, 이 표면은 패드 또는 다이 부착 위치로 사용될 수 있다.
② 웨이퍼 필름 전처리 : 웨이퍼 필름은 다이와 기판 사이에 사용되는 접착성 있는 필름이다. 웨이퍼 필름은 전처리 단계를 거쳐야 한다. 이 단계에서는 웨이퍼 필름을 적절한 크기로 잘라내고, 필요한 특성을 갖도록 처리한다. 전처리에는 필름 절단, 세척, 건조 등의 과정이 포함될 수 있다.
③ 칩의 공급 및 접합 : 다이(칩)은 기판에 부착되는 작은 반도체 칩이다. 이 단계에서는 다이를 적절한 위치에 공급하고 기판에 접합한다. 접합은 웨이퍼 필름을 사용하여 다이를 기판에 안정하게 고정하는 과정을 의미한다. 이 단계에서 정확한 위치 제어와 접착력을 유지하는 것이 중요하다.
④ 기판 배출 : 언로더는 인텍스 외부 레일로부터 기판을 상부 방향으로 배출시켜 매거진에 넣는다.
▶3. 다이 부착(Die Attach) 장비의 핵심기술(Die Ejector)
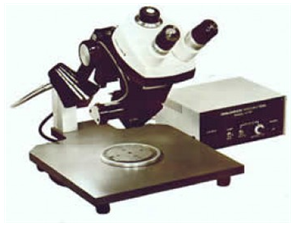
① 다이 분출기(Die Ejector) : 소잉(절단)이 완료된 웨이퍼 칩은 마운팅 테이프에 고정된 상태이며, 칩 하부에서 분출 핀(ejector pin)으로 칩을 밀어 올려주며, 다이 분출기(이젝터)는 웨이퍼 확장기가 웨이퍼 링을 아래 방향으로 잡아당겨 웨이퍼 필름의 장력을 증가시킬 수 있다.
② 다이 픽업(Pick up) : 칩 상부에서 진공을 이용하여 칩을 집는다.
③ 다이 맵핑(Mapping) : 정상과 불량 칩 분류 방법은 잉크로 표시하여 구분한다.
▶4. 와이어 본딩 장비기술
① EFO(Electronic Flame-off, 전기적 불꽃) 장치에 의한 FAB(Free Air Ball) 형성
: 와이어 신뢰성 확보를 위해 와이어와 EFO 막대기(wand) 간 간극(gap) 및 꼬리(tail) 길이 제어가 중요한다.
② 모세관(Capillary) 동작 : 클래퍼가 열리면서 모세관이 아래 방향으로 패드 표면가지 이동하여 볼과 패드 면이 접촉하며, FAB는 칩의 중앙에 위치하고, 충격 하중을 가하면서 본딩을 진행한다.
③ 1차 본딩 동작 : 열 블록에 의한 가열, 하중 본딩 및 초음파 진동이 가해지면서 1차 본딩이 이루어지며, 볼 형상 유지를 위해 초기 충격과 하중을 조절하는 것이 중요한다.
④ 2차 본딩 동작 : 볼 본딩 이후 와이어를 리드 프레임(또는 주 PCB)에 접합시키는 기술로써 모세관과 역 방향으로 이동하면서 루프를 형성한 다음, 리드 프레임으로 이동하여 가열, 하중 및 초음파 기술로 바느질 방식 본딩을 진행한다.
⑤ 와이어 본딩 재 작업 준비 : 본딩 완료 후 무세관이
※8. 범핑 장비기술
▶ 범핑 장비
① 세척 장비 - 범핑 공정에서 사용되는 세척 장비는 부품 또는 기판의 표면을 깨끗하게 만들기 위해 사용된다. 이 장비는 이온화된 물, 용매 또는 산성 또는 알칼리성 용액을 사용하여 불순물, 오염 또는 남은 잔여물을 제거한다. 세척은 부착 전 표면의 깨끗함과 부착 품질을 보장하기 위해 중요한 단계이다.
② 열처리 장비 - 범핑 후 다이 또는 부품을 열처리하는 장비이다. 열처리는 부착된 다이 또는 부품의 기계적 강성성 및 안정성을 향상시키기 위해 수행된다. 열처리는 일반적으로 고온로나 가열로를 사용하여 정확한 온도와 시간 조건에서 수행된다. 열처리는 다이와 기판 간의 접착력을 향상시키고 내부 응력을 제거하여 제품의 신뢰성을 향상시킨다.
③ 물리적 증착 장비 - 물리적 증착 장비는 범핑 공정에서 다이나 부품에 얇은 금속 층을 증착하기 위해 사용된다. 이 장비는 대상 부품을 진공 상태로 유지하고 금속 증착 소스에서 기체 상태로 증착된 금속을 표적 부품에 증착한다. 이를 통해 부착된 다이 또는 부품에 전기적 연결성과 보호를 제공하는 금속 층이 형성된다.
④ PR 도포, 노광 및 현상 장비 - PR(Positive Resist) 도포, 노광 및 현상 장비는 반도체 패키징 공정에서 사용되는 장비이다. 이 장비는 PR 재료를 부착 대상에 도포하고 노광 공정을 통해 패턴을 형성한 후, 현상 공정을 통해 패턴을 완성한다. 이 단계에서는 반도체 패키지의 패턴화된 구조 또는 회로를 형성하여 전기적 및 기계적 기능을 구현한다.
⑤ 전해 도금 장비 - 전해 도금 장비는 범핑 공정에서 사용되며, 다이나 부품의 표면에 금속 도금을 수행하는 장비이다. 전해 도금은 전해질 용액을 사용하여 부착된 다이나 부품의 표면에 금속 이온을 전기적으로 증착시킨다. 이를 통해 다이나 부품의 전기적 연결성을 향상시키고 내식성, 내구성을 제공하는 금속 층이 형성된다. 전해 도금 장비는 정확한 도금 조건과 고품질의 도금 층을 형성하기 위해 전류, 온도, 시간 등을 제어한다.
⑥ PR Strip 장비 - PR Strip 장비는 범핑 공정의 마지막 단계 중 하나로, 패키지의 표면에서 PR 재료를 제거하는 장비이다. PR 재료는 전형적으로 화학적인 용액이나 용매를 사용하여 제거된다. PR Strip 장비는 부착된 다이나 부품의 표면을 깨끗하게 만들어 다음 공정에 영향을 주지 않도록 한다. 이를 통해 패키지의 신뢰성과 기능을 보장할 수 있다.
⑦ 금속막 식각 장비 - 금속 층을 패턴화하기 위해 사용된다. 이 장비는 금속 층의 특정 부분을 화학적인 용액 또는 가스를 사용하여 제거하는 프로세스를 수행한다. 이를 통해 부착된 다이나 부품에 원하는 금속 패턴을 형성할 수 있다. 금속막 식각 장비는 정확한 제어와 패턴 정의를 통해 고성능 반도체 패키지의 제조에 중요한 역할을 한다.
⑧ IR 리플로우(Reflow) 장비 - 다이나 부품의 접착을 강화하기 위해 사용되는 장비이다. 이 장비는 적외선(IR) 열을 사용하여 다이와 부품 사이의 접착제를 녹이고 다이를 부착 대상에 고정하는 프로세스를 수행한다. 이를 통해 다이와 부품 간의 강력한 접착이 형성된다.
⑨ AVI(Auto Visual Inspection) - 범핑 공정에서 사용되는 자동 시각 검사 장비이다. 이 장비는 다이나 부품의 외관적인 결함, 불량, 오염 등을 감지하고 검사하는 역할을 수행한다. AVI 장비는 일반적으로 고해상도 카메라와 이미지 처리 알고리즘을 사용하여 다이나 부품의 표면을 검사하며, 결함이나 불량을 식별하여 제거 및 보완 작업을 수행한다. 이를 통해 패키지의 품질을 향상시키고 불량품을 제거하여 생산성을 향상시킨다.
※9. 몰딩(Moiding) & 마킹(Marking) 장비기술
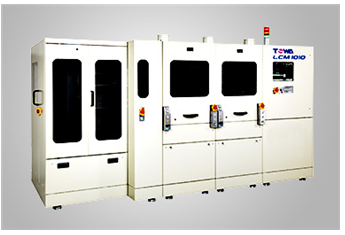
▶1. 몰딩 장비 Flow
① 매거진은 본딩이 완료된 리드 프레임을 저장, 공급한다.
② 리드 프레임 이송부은 리드 프레임을 로더에 공급된 상태로 정렬한다.
③ 로딩 장치는 리드 프레임 이송부 상의 리드 프레임과 탭 슛트에 정렬된 EMC를 공급 받아서 금형에 로딩한다.
④ EMC를 개별 분리한 후, EMC를 탭 슛트로 이송하고 로더에 공급한다.
⑤ 가압부(Press)의 상하부 로더로부터 상승 레인(lift lane)과 EMC를 공급받아 성형한다.
⑥ 언로딩 장치는 성형이 완료된 자재를 운반하는 역할을 한다.
⑦ 이송부는 언로더로부터 받은 제품과 컬을 분리한다.
⑧ 픽업부(Pick-up)는 캐리어로부터 성형 완료 자재를 받아 적재기 매거진에 적재하는 역할을 한다.
▶2. 마킹 장비의 요소기술
: 마킹 장비는 로더, 마킹 PC, 인텍스 유닛, 비전 유닛 및 오프 로더 부로 구분할 수 있다.
① 로더 부 : 제품을 로딩하기 위한 장치로 매거진이 엘리베이터까지 가도록 하는 카세트 벨트, 매거진을 고정시키는 카세트 그리퍼, 마킹 전 자재의 매거진을 잡아서 올려주는 리프트, 마킹 전 프레임을 하나씩 인서트로 밀어주는 엘리베이터 푸셔, 푸셔가 밀어준 프레임을 앞으로 밀어주는 보조기능을 하는 롤러, 인서트가 인텍스 앞까지 밀어주는 인서트로 구성된다.
② 핸들러 및 마킹 PC : 자동화된 부품을 처리하고 마킹 프로세스를 제어하며 관리하는 컴퓨터 시스템으로 레이저 빔을 방출하고 원하는 위치까지 전달시키는 레이저 헤드와 빔을 스캔하는 마킹 시스템, 그리고 전력 공급장치, 냉각장치, 마킹 전용 소프트웨어가 탑재된 PC, 스위치, 전류 제어장치 등으로 구성된다.
③ 인텍스(Index) 유닛 : 프레임 또는 작업 대상을 정확한 위치로 이동하고 정렬하는 역할을 수행한다. 마킹부로 이동시키는 리어 인덱스 핑거, 상하 동작을 위한 인덱스 상/하, 기타 스테이션 상/하, 주입구 비전, 마크 비전, 레일/메뉴얼 버튼이 있다.
④ 오프 로딩 : 마킬 공정 후 프레임을 장비 외부로 배출한다.
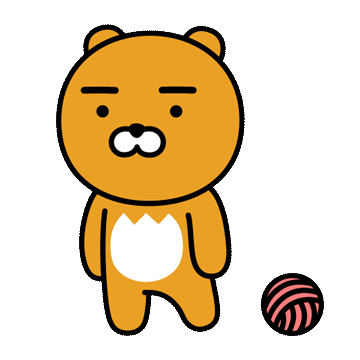
'Semiconductor > Semiconductor Fabrication' 카테고리의 다른 글
[반도체 공정] Moore's Law & Huang's Law (무어의 법칙 & 황의 법칙) (0) | 2024.05.15 |
---|---|
[반도체 공정] 플라즈마 공정, 플라즈마 장비 (0) | 2024.05.15 |
[반도체 공정] 이온 주입 공정, 이온 주입 장비 (0) | 2024.05.14 |
[반도체 공정] 박막 공정, 박막 공정 장비 (0) | 2024.05.13 |
[반도체 공정] 웨이퍼 제조, 웨이퍼 제조 장비 (0) | 2024.05.07 |
전자공학 블로그에 오신 것을 환영합니다! 최신 기술 동향, 회로 설계, 반도체 및 전자 부품에 대한 유용한 정보와 실습 팁을 제공합니다.